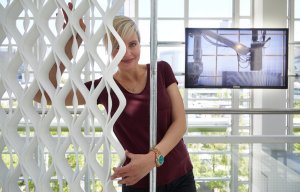
New dates for Techtextil and Texprocess
Opinion
Innovation award winners reflect response to increasing demands on developers of sewing and apparel technology and machines for processing technical textiles.
28th June 2022
Adrian Wilson
|
Frankfurt, Germany
Four developers of advanced garment making-up and technical textile component assembly technologies received 2022 Texprocess Innovation Awards at the Frankfurt show last week (June 21-24).
Cold glue
Welding and sewing machine manufacturer Vetron Typical Europe has developed a new type of cold gluing robot which for the first time makes it possible to automatically seal seams with adhesive tape on the reverse side of a garment or component.
Cold gluing – for decorative seams on dashboards in the automotive industry, for example, or closing seams in outdoor clothing – is state of the art in many industries, but because the adhesive tape has to be cut off manually, has not before been combined with the high demands of process automation. The new Vetron robot, presented publicly for the first time at Texprocess 2022, is already attracting great interest – especially from the automotive industry.
Reinvented embroidery head
ZSK Stickmaschinen, headquartered in Krefeld, Germany, has developed a new type of embroidery head for single and multi-head embroidery machines. The R-head is designed to achieve embroidery speeds of up to 2,000 stitches per minute. By comparison, traditional multi-head embroidery machines currently achieve speeds of up to a maximum of 1,200 stitches per minute. With this development, ZSK is enabling a new dimension of productivity with higher embroidery precision and reliability. The R-head also significantly reduces noise emissions compared to current embroidery heads and customers should also be able to replace it themselves if necessary.
AW-3S
Juki Central Europe in Poland has developed the AW-3S automatic bobbin thread winding and feeding device which not only automatically calculates the amount of bobbin thread required when loading a sewing pattern, but can change the sewing thread automatically. As a result, it not only increases productivity, but saves operators having to change the sewing thread manually, reducing fatigue and allowing them to concentrate more on production and quality control.
Qondac Guided Working
Dürkopp Adler, headquartered in Bielefeld, Germany, has developed the new Qondac Guided Working software module. In interaction with programmable sewing machines, it provides the perfect link between planning, operating personnel and machine by supporting processes from production planning to the last work step at the final workstation.
In addition, additional manual workstations or conventional sewing machines can also be easily integrated into the network.
Challenges
“The increasing demands on manufacturers of sewing and apparel technology and on machines for processing technical textiles, to automate and digitise production processes – while also responding to an increased focus on regional production – can contribute to greater supply chain transparency,” said Elgar Straub from the VDMA trade association during the awards ceremony in Frankfurt. “Mechanical engineering and technology providers are the enablers for solutions to today’s biggest challenges – sustainability, flexibility and regionalisation.”
Business intelligence for the fibre, textiles and apparel industries: technologies, innovations, markets, investments, trade policy, sourcing, strategy...
Find out more