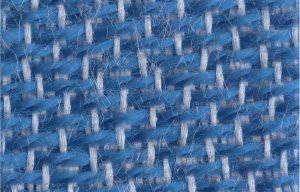
Digital technology weaves its way into custom design
Green Eileen decided to partner with the project and has donated all of the garments used to date.
25th April 2017
Innovation in Textiles
|
Ithaca, NY
The average American goes through roughly 70 pounds of clothing each year, creating approximately 21 billion pounds of clothing sent to landfills – 5% of all landfill waste, according to the Council for Textile Recycling.
A multidisciplinary Cornell design and research team has developed a unique fabric-shredding machine in hopes of a zero-waste solution for the textile industry.
“The Fiberizer project aims to put textiles, destined for the landfill, to better use as materials to create new textiles and other products, reducing the consumption of natural resources and diverting unwanted clothing away from becoming waste,” said Tasha Lewis, assistant professor of fibre science and apparel design in the College of Human Ecology.
The Fiberizer v.2, its official name, was built from the original proof-of-concept project Fiberizer v.1, which was funded by a grant from the Environmental Protection Agency and Cornell’s Atkinson Center for a Sustainable Future. To fund the v.2, Lewis secured a Walmart Foundation US Manufacturing Innovation Fund grant.
“The grant’s call for proposals also requested applicants to name industry partners that we could work with on research,” she said. “We reached out to Eileen Fisher’s Green Eileen [recycled clothing line], who we have discussed potential projects with in the past.” The Irvington, New York-based apparel company is known for embracing simplicity and sustainability.
Green Eileen decided to partner with the project and has donated all of the garments used to date. A goal of the partnership is to give Green Eileen a variety of fibre samples based on the inventory donated, along with end-product recommendations for the types of fibres generated, helping the company achieve its objective of having a transparent supply chain by 2020.
The Fiberizer takes old garments, which may not be usable or suitable for resale, and turns them into a fibrous mass. The material generated can be turned into something of value the apparel industry can use or reuse, and allows new consumer products to be created.
“The industry today already has industrial-grade fabric cutters or shredders that do cut up mixed amounts of clothing that is not sellable or usable,” said Lewis. “Many in the industry simply throw it all in and chop it, mixing all kinds of materials together and turning it into what could become carpet padding, insulation in a car, or something similar.”
Lewis explained that the Fiberizer was designed to allow users to take into consideration what a particular textile is made of, the value of the fibre content and how it is constructed, such as knit or woven material. “This allows for a type of refurbished textile production from reclaimed apparel that can be used for new garments by the industry and create additional revenue streams for apparel, while at the same time reducing waste and promoting sustainability,” she said.
Lewis assembled a collaborative, multidisciplinary design and research team for the Fiberizer project, with students from fibre science and apparel design, design and environmental analysis, physics, mechanical and aerospace engineering, and materials science and engineering.
Through design and creation, and development and enhancement of the machine, the team has been working to explore issues, come up with new ideas and identify the potential for a closed-loop supply chain that supports new product manufacturing, enables additional revenue streams from reclaimed apparel, and tackles the environmental problem of post-consumer textile waste.
“Through modification and refinements in its design, we can use different cutting blades for different fabrics, because we’re finding it’s not a one-size-fits-all solution,” Lewis said. “We want to know, if the mass material comes out a certain way, what is the perfect application for that particular fibre quality grade of material?”
Business intelligence for the fibre, textiles and apparel industries: technologies, innovations, markets, investments, trade policy, sourcing, strategy...
Find out more