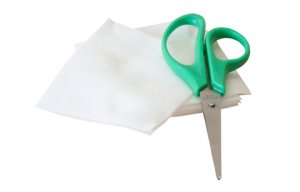
Suominen introduces Genesis Pro All Purpose nonwoven substrate
Opinion
Comparisons with incumbent products are unhelpful in what should be should be considered an entirely new and value-added class of materials, panellists stress.
26th February 2024
Adrian Wilson
|
Online
In an illuminating webinar organised by Material Innovation Initiative (MII), three panellists from next-generation fibre developers – AMSilk, Circ and Kintra Fibers – spoke of the challenges of getting to industrial scale and the importance of cementing strong partnerships with both brands and mills.
The webinar was timed to tie-in with the MII’s just-published free report What Makes Silk, Silk? Revisited 2023, which explores the luxury fibre’s unique properties and aims primarily to inspire a new generation of scientists and entrepreneurs to develop high performance and sustainable next-generation silk materials.
Biosteel
AMSilk, based in Neuried near Munich, Germany, was founded in 2008 and is the producer of unique spider silk made with recombinant biotechnology, by combining e-Coli bacteria with the spider silk protein.
The company’s senior product manager for fibres Martin Lankes observed that the company’s initial focus was on high performance properties, but over the years, the emphasis has shifted, and the fact that the company’s bioengineered fibres – branded Biosteel – are based on renewable raw materials, biodegradable, fully recyclable and with a lower carbon footprint than other high performance fibres, has assumed equal, if not greater importance.
A shift from performance to purpose was agreed by all speakers to have been general in new textile industry raw material developments.
Biosteel is a high performance filament fibre that is thinner and more delicate than traditional animal-based silk and is biodegradable in marine, anaerobic and aerobic conditions. In addition, it is hypoallergenic and bacteriostatic and can be dropped into the existing value chain for knitting and weaving to create a variety of applications ranging from a silk-like fabric based on superfine yarns to materials for applications such as composite reinforcements or sport shoes made from highly resistant yarns.
In medical use, Biosteel is being used to coat breast implants to prevent infection and reduce post-operative complications.
Kintra
Kintra Fibers, based in Brooklyn, New York, has developed a proprietary biobased and biodegradable polyester that is highly tuneable in terms of its properties and can be produced on the same equipment as PET polyester resins and fibres, but operating at lower temperatures, enabling a 20% reduction in energy usage.
Co-founder and CEO of Billy McCall explained that Kintra products have been intentionally designed to biodegrade in aerobic environments as a means of addressing microfibre pollution within wastewater treatment facilities, mimicking how natural fibres biodegrade.
Kintra has garnered interest from over 500 apparel brands and manufacturers and has launched pilots with global brands, including Bestseller, H&M, Inditex and Reformation, who are prototyping the materials in their product lines.
Speaking of the problem of scaling up, McCall said that getting to that stage could be a massive cash burner.
“The material inputs can become different and if not 99.9% identical, discrepancies become magnified and one bad batch is a lot of money,” he said.
Circ
Circ, based in Danville, Virginia, has developed a platform to successfully separate polycotton blended textile waste and recover both the cellulosic and synthetic fibres. The company was named as one of the 15 finalists for the 2023 Earthshot Prize – the global environmental award that celebrates and champions innovators focused on solving global climate challenges.
“Our patented hydrothermal process turns the polyester fibres into a liquid, completely separating them from the cotton fibres,” explained Shannon Parker, the company’s director of industry engagement and impact strategy.”
Preserving and separating the polyester without damaging the cotton allows both materials to be reused in the production of new textiles, while also substantially reducing carbon emissions.
New class
All three speakers agreed that comparing these next-gen materials to incumbent products is unhelpful, and instead, they should be considered an entirely new and value-added class of materials.
The MII’s report showcases a number of other material innovators who are successfully developing next-gen silk and other fibres through various different approaches, including Alt Tex, Eastman Naia, ettitude, Lenzing, Nanolose, Orange Fiber, Renewcell, Rubi Laboratories, Spidey Tek, Spiber and Tandem Repeat.
“Fashion designers love to use silk,” says Thomasine Dolan Dow, director of materials innovation and design at MII. “It’s one of the most luxurious and ancient textile fibres and its smooth, continuous filament gives silk yarn some unique properties such as strength, elasticity and resistance to pilling. The silk industry accelerates climate change and environmental degradation, relies on inhumane and unsustainable animal agricultural practices and offers few protections for workers in processing plants. Popular synthetic alternatives to silk like polyester and nylon contain microplastics which accumulate and persist in ecosystems for hundreds of years. Next-gen materials are a solution to these problems and it’s very exciting to see so many innovators developing them.”
The MII’s report can be accessed here, and the webinar can be viewed here.
Business intelligence for the fibre, textiles and apparel industries: technologies, innovations, markets, investments, trade policy, sourcing, strategy...
Find out more