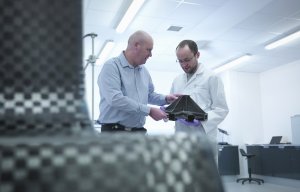
Sigmatex recognised for sigmaRF fabrics
Naturally occurring enzyme can speed a reaction in which CO2 and water will turn into bicarbonate.
25th August 2023
Innovation in Textiles
|
Raleigh, NC, USA
North Carolina State Wilson College of Textiles researchers are working on the development of carbon dioxide (CO2) capture filters including a cotton fabric and an enzyme called carbonic anhydrase – one of nature’s tools for speeding chemical reactions.
Initial laboratory testing suggests that scaled up, it represents a step forward in the development of a possible new technology that could reduce CO2 emissions from biomass, coal or natural gas power plants.
“With this technology, we want to stop carbon dioxide emissions at the source, and power plants are the main source of CO2 emissions right now,” said Jialong Shen, postdoctoral research scholar at NC State. “We think the main advantage of our method compared to similarly targeted research is that it could be easily scaled up using traditional textile manufacturing facilities.”
Carbonic anhydrase can speed a reaction in which carbon dioxide and water will turn into bicarbonate.
To create the filter, the researchers attached the enzyme to a two-layer cotton fabric by immersing it in chitosan, which acts like a glue.
The researchers then ran a series of experiments to see how well their filter would separate an air mixture of CO2 and nitrogen, with success rates of 52.3% CO2 with a single-stacked filter and 81.7% with a double-stacked filter. While the findings are promising, the filter still needs to be tested against the faster air flow rates that are used in commercial power plants. For comparison, a full-scale operation would need to process more than 10 million litres of flue gas per minute. The researchers are working with collaborators to test at a bigger scale and to compare their technology to other comparable technologies.
3D printing
In related work, the researchers have also recently demonstrated that it’s possible to make CO2 filters using 3D printing and a hydrogel material that can hold the carbonic anhydrase.
“This manufacturing process using 3D printing makes everything faster and more precise,” said Shen. “If you have access to a printer and the raw materials, you can make this functional material.
“We formulated the hydrogel in a way that would be mechanically strong enough to be 3D printed, and also extruded into a continuous filament and the inspiration behind our design was our own cells, which have enzymes packed into compartmentalised spaces, filled with a fluid. That kind of environment is good for helping enzymes do their job.”
The researchers tested the properties of the material to understand how well it would bend and twist, and investigated the filter’s carbon capture performance. In a small-scale experiment, they found the filter captured 24% of the carbon dioxide in a gas mixture. While the capture rate is lower than what they’ve achieved in other designs, the filter was less than an inch in diameter and could be made larger and in different modular shapes in order to stack them in a tall column to increase the capture efficiency.
The researchers also tested the filtration durability of the material, and found it retained 52% of its initial carbon capture performance after more than 1,000 hours.
Business intelligence for the fibre, textiles and apparel industries: technologies, innovations, markets, investments, trade policy, sourcing, strategy...
Find out more