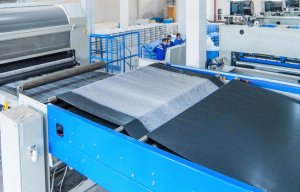
Flying start to the year for Andritz
Opinion
Despite having only really emerged since the 1940s, the value of the worldwide composites market is now estimated to be worth an annual €77 billion and to account for around 550,000 jobs worldwide.
9th April 2013
Adrian Wilson
|
Paris
Despite having only really emerged since the 1940s, the value of the worldwide composites market is now estimated to be worth an annual €77 billion and to account for around 550,000 jobs worldwide.
This year’s JEC Europe Composites show in Paris – despite being blighted by travel difficulties due to unseasonably heavy snow in France – demonstrated the opportunities for technical textiles in a market which continues to expand rapidly.
It coincided, for example, with the 100th Airbus A380 being delivered to Malaysia Airlines, providing an opportunity for a number of companies involved in its development to celebrate.
Some 25% of the A380 is produced using composite materials, while it is projected that 53% of the next-generation A350 plane will be composite-based, including key elements such as the wings and fuselage.
For Hexcel Corporation, headquartered in Stamford, Connecticut, USA, the Airbus A350 has represented a contract worth between $4-5 billion to date, with over $4 million worth of carbon fibre prepregs – fabrics impregnated with resins – and associated products on each plane.
The A350 composite structures built by Airbus include entire fuselage panels, keel beams and wings, with the lower wing covers being the biggest single civil aviation parts ever made from carbon fibre – measuring 32 metres long by six metres wide.
Airbus says that composite materials maximise weight reduction – typically 20% less weight than aluminium – and are known to be more reliable with a longer lifespan than other traditional metallic materials, reducing aircraft maintenance costs and frequency of inspections during service.
There is massive investment being placed in developing technologies to improve the speed of composite manufacturing, since it is more complicated than traditional metallic materials. However, the advantage to the material is that integrated structures and systems can be produced more easily, leading to cost reduction at the assembly stage.
According to PRF Composite Materials, based in Poole, Dorset, UK, however, the focus in prepreg development has largely been on the resin systems, with very few advances made in the actual fabric reinforcements in recent years.
“We believe that there is far more to be done by using the latest fabric technology in the manufacture of prepreg,” says MD Robert Burnell. “This is central to our aims.”
PRF has just installed a new prepreg line which will be operational by the end of May 2013. With a capacity of over a million linear metres at 1.5m wide, the new line will be suitable for large quantities as well as small runs of speciality materials.
French company Chomorat, meanwhile, introduced its new TPreg range of fabrics for the production of thermoplastic composites, which it says have many advantages in respect of the speed at which they can be converted, as well as their formability and recycling options.
“TPreg is a conformable reinforcement that preserves perfect orientation of the fibres,” says R&D manager Philippe Sanial. “It can be designed with a diversity of materials – carbon, glass etc. – and in different widths. With various impregnation levels in development, the range opens up new technical and lower cost options for the market.”
Another UK company, NetComposites, unveiled a flax fabric/polyfurfuryl alcohol resin prepreg which is 100% bio-derived as a more sustainable alternative to glass-reinforced products.
Again, a twistless technology is used to convert the flax and provide high levels of performance and processability. This is the first time that flax and polyfurfuryl alcohol resins have been combined to provide a sustainable, semi-structural, fire-resistant material and reflects the strong developments taking place in the use of natural fibre fabrics as the basis for composites.
At present, natural fibres and fabrics are estimated to have an 11% share of those going into composites, and the stated goal of CELC – the European Confederation of Flax and Hemp – is to double this to 22% by 2020.
The path to success, however, is not without obstacles, and some are as a result of the properties of flax fibres themselves, most notably in respect of strength and moisture absorption.
Nevertheless, there were some impressive examples of new products based on them at JEC 13, including the new Z-Concept semi-inflatable boat, jointly developed by Paris-headquartered Zodiac Recreational and fellow French company the Dehondt Group, which received the 2013 JEC Composites Innovation Award in the Sports and Leisure category.
The Z-Concept’s entire hull is one-step moulded, with the flax fabric reinforcement incorporated on its deck side.
The greenOne technology of Notox, based in Anglet, France, combines technical flax fabrics –twillweave, unidirectional and bi-axial – with recycled EPS foam impregnated with biosourced epoxy resin. It is being employed in the company’s range of high-end surfboards. From a performance point of view, these ultra-light boards have greatly improved vibration damping properties as well optimised floatability, speed and thrust.
Notox is now teaming up with Norafin, based in Müllheim, Germany, to explore the potential of flax nonwovens as the basis for future boards.
Two other French companies, Ecotechnilin and Depestele, introduced Lincore ML a technical-flax laminate fabric with a nonwoven core layer available in rolls or sheets.
The new needlepunch-bonded product exists in a 100% natural version or one that incorporates thermoplastic filaments (e.g. PP, PLA, PA). The ready-to-use sandwich product can be adapted to standard composites processes.
Combined with its low density, the laminate structure’s mechanical properties make it suitable for applications in a number of industrial sectors.
All of these developments, and many more that were to be viewed at JEC 13, represent the current key drivers for the European composites market – environmental impact reduction and cost savings.
Finally, it would be remiss not to mention the special Innovation Award that was made to BMW in recognition of its pioneering i LifeDrive programme which is kick-starting the move towards composites replacing steel in cars, just as they are already doing in planes.
In the early 1930s, BMW says progress in metal cutting and a desire for lighter, more powerful car gave birth to an innovation that would dominate the industry for many decades – the integral monocoque body.
Three quarters of a century later, at the dawn of the electric vehicle era, the BMW i team has again faced the challenge of how to reduce a vehicle’s weight – this time to accommodate the battery for an electric motor. The result is the world’s first body architecture specifically designed and purpose-built for the series production of electric vehicles – the LifeDrive concept. In contrast to vehicles with a monocoque body, the LifeDrive architecture is made up of two separate functional units.
The upper module consists mainly of a high-strength and extremely lightweight passenger cell made of carbon fibre reinforced plastic (CFRP) which not only compensates for the extra weight of the battery unit, but also lowers the vehicle’s centre of gravity to make it a more dynamic vehicle to drive. A lightweight design is not the only benefit. The carbon-fibre passenger cell is exceptionally rigid and strong and in the case of the BMW i3 there is no space-consuming tunnel running through the middle of the vehicle, since all the power components are housed in the drive module.
Up to 2020, BMW anticipates a worldwide market share of 4 to 8% for electric vehicles. In addition, together with the German Government, BMW is adhering to the target of one million electric vehicles on German roads by 2020.
Business intelligence for the fibre, textiles and apparel industries: technologies, innovations, markets, investments, trade policy, sourcing, strategy...
Find out more