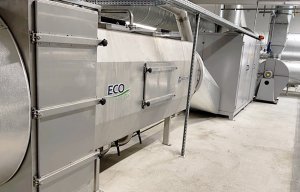
Feinjersey minimises energy consumption with Brückner
Hans-Peter Prinzen, Head of R & D at A.Monforts Textilmaschinen, talks about how the finishing and coating of fabrics are amongst the most energy-intensive steps in the production of textiles.
17th July 2015
Innovation in Textiles
|
Mönchengladbach
In a recent VDMA presentation, Hans-Peter Prinzen, Head of R & D at A.Monforts Textilmaschinen, stated that the finishing and coating of fabrics is amongst the most energy-intensive steps in the production of textiles. Energy costs account for a considerable portion of the production costs as significant heating energy is required for drying, finishing and fixing processes, he said. The following is a summary of Mr Prinzen’s presentation.
Using a heat recovery system, part of the energy in the exhaust air can be used in a heat exchanger to preheat the fresh air. Furthermore, the cooling of the exhaust air allows finishing agents, oils and waxes to recondense and be separated, further aiding the environment.
Without a heat recovery system, the hot exhaust air is released unused into the atmosphere.
Monforts reacted to this situation several years ago and has developed three variants of heat recovery systems:
All three variants operate without the costly intermediate storage of the heat. The savings effect is achieved by the direct heating of the fresh air.
Today integrated heat recovery systems form an integral part of the Monforts standard product range.
Whilst new Monforts ranges generally have a heat recovery system that is integrated into the existing range, there are still a large number of older Monforts ranges in operation worldwide.
“It is for these plants that we have developed the Energy Tower,” said Hans-Peter Prinzen.
Energy Tower is a stand-alone solution that can be can be flexibly deployed – even on third-party machines.
The Eco-Booster is an automated variant. This heat wheel cleans itself fully automatically during the on-going finishing process. The system does not become soiled, so there are no’ standstill’ times.
In the integrated heat recovery system, part of the thermal energy in the exhaust air is recovered in low-maintenance tubular heat exchangers so that the fresh air preheated to, for example, around 90°C. It then only has to be heated to 150°C.
As a result, the high drying temperature is reached more quickly and the energy consumption is reduced. The energy savings can be as much as 30 %.
The Energy Tower is a stand-alone solution for retrofitting in machines that do not have an integrated heat recovery system. Older ranges are still in operation in many facilities.
The Energy Tower as a retrofit module with low-maintenance tubular heat exchangers can be flexibly deployed and functions even on third-party machines. It can be connected to relaxation dryers, infrared predryers, hotflues, continuous dyeing ranges and condensation ranges or retrofitted on existing stenter ranges.
The Eco-Booster is an automated solution for the production process. The heat wheel allows computer-controlled optimisation of the heat exchanger output relative to the prevailing exhaust airflow.
This optimised efficiency further reduces the process costs.
The Eco-Booster operates fully automatically so that the operator is relieved of all other duties. ‘Standstill’ times for maintenance are also eliminated, as cleaning is performed by an integrated high-pressure cleaner.
Compared with purely static heat exchanger modules, the new module cleans itself independently during operation.
“We calculate precisely for the customer when the investment in a heat recovery system has paid for itself,” said Hans Peter, adding, “Customers are often amazed that a payback is achieved within two years.”
“But this should not be surprising. Energy is a major cost factor when it comes to textile finishing. Two-thirds of the drying energy is used for evaporation heat.
“Up to 30 % of the heating energy can be saved with the Energy Tower or the Eco-Booster.”
As the energy costs are a significant factor in the drying process, that represents a considerable saving.
The Eco-Booster also allows a higher availability of the range and increases productivity thanks to its automated cleaning process. This again saves costs.
Furthermore, a heat recovery system ensures that no hot exhaust air is released unused into the atmosphere; reducing the impact on the environment.
Business intelligence for the fibre, textiles and apparel industries: technologies, innovations, markets, investments, trade policy, sourcing, strategy...
Find out more