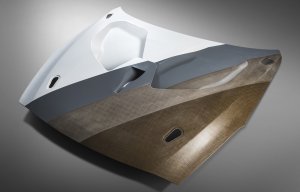
Sustainable bio-composites from Retrac
Opinion
Adrian Wilson, who attended the Filtrex 2014 conference organised by EDANA, says nonwoven media both for fuel and air filtration in vehicles are having to become increasingly sophisticated nowadays
3rd November 2014
Adrian Wilson
|
Berlin
For differing reasons, nonwoven media both for fuel and air filtration in vehicles are having to become increasingly sophisticated.
New injection technology – particularly for diesel engines and those for mass transportation systems – has created a greater need for cleaner fuel and as far as fuel filters are concerned, moisture is becoming as much of a problem as solid particulates.
“The injection technology in common rail systems already operates at 2,500 bar pressure and now Bosch, for one, is talking about going up to 3,000 bar, which will require even cleaner fuels,” said Harald Banzhaf, director of R&D in liquid filter elements at Mann+Hummel, headquartered in Ludwigsburg, Germany.
Speaking at the recent EDANA Filtrex 2014 conference which took place from October 1-2 in Berlin, Germany, he added that in diesel engines – and those with a percentage of bio content which are even more vulnerable – water removal now needs to be the first priority in filter systems.
Water gets into the fuel tank and diesel fuel in a number of ways, but the consequences include corrosion and cavitation on injectors, valves and the injection pump – which can ultimately lead to a system failure. In addition, free water can cause microbiological growth and corrosion which frequently lead to premature blockage of the fuel filter or damage to the filter housing.
In the past, single-stage concepts were sufficient to meet the requirements for water separation efficiency, but in order to respond to these new demands, Mann+Hummel has developed a three-stage filtration concept in its latest Multigrade filtration modules.
In these filters, the fuel flows from the outside to the inside of the element. In the first stage, solid particles are filtered out and it’s crucial that the coalescer and the hydrophobic fabric are not contaminated by particles. The coalescer then retains the water droplets and combines them to form much larger drops. In the third stage, a hydrophobic screen fabric prevents the drops from following the fuel into the injection system. The separated water is collected in the filtration module, detected there and emptied out either manually or automatically. As a result of the high water separation efficiencies that can be achieved, the injection systems and commercial vehicle engines are reliably protected.
Andrew Shepard, director of global market management at Hollingsworth & Vose Engine and Filtration noted that stringent new regulations – especially in Europe – are currently impacting all along the supply chain in respect of emissions requirements and at the same time there is pressure on filter makers to provide media that allow longer intervals between servicing.
At the same time, automotive engine technology is increasingly incorporating highly sensitive sensor technologies and as a result, the installation space for components such as air filters under the bonnet has been shrinking.
Three key developments are discernible in response to these challenges – the incorporation of nanofibre layers or coatings, the emergence of hybrid products combining cellulose and synthetic nonwovens, and advanced pleating.
Hollingsworth & Vose NanoWave filter media, for example, is an extended surface area, multi-layer filtration media for employing nano and coarse fibre layers to deliver 2.4 times the surface area of normal flat sheet media.
Mann+Hummel’s nanofibre media in its Micrograde A-NF series, meanwhile, is also used in the new VarioPleat air filter series for commercial vehicles to achieve higher filter fineness values and protect the turbocharger and air mass flow meter, without reductions in service life. VarioPleat was developed specifically to provide maximum filtration performance in a very compact space.
Both Ahlstrom and Johns Manville introduced sophisticated new hybrid products at the Berlin event.
Ahlstrom’s latest Pleat2Save HVAC air filter has a patent pending engineered structure consisting of a combination of polyester fibres and glass layers. This, said Ina Parker, product manager for the company’s Advanced Filtration business, does not involve lamination, but is manufactured as a single web via the wet-laid process.
The key value proposition of Pleat2Save, she added, was in its robustness – it has a tensile strength around 2.5 times higher than microglass alternatives allowing for excellent processing performance during pleating.
So too, do the glass nonwoven filter media being manufactured by JohnsManville, a company which has proprietary technology for the production of both glass and spunbond nonwovens and is currently introducing a hybrid product comprising glass mat and polyester/PBT bicomponent spunbond fibres.
JohnsManville market and product platform manager for filtration Jörg Meier disclosed the company’s highly technical internal process for testing the ability of such materials to withstand pleating and harsh operating conditions – dropping a hammer on them from a suitable height!
Business intelligence for the fibre, textiles and apparel industries: technologies, innovations, markets, investments, trade policy, sourcing, strategy...
Find out more