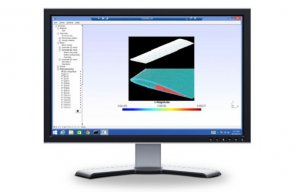
Opterus R&D licenses SwiftComp software
New digital technologies to support more sustainable bulk production.
4th December 2023
Innovation in Textiles
|
Holmfirth, UNited Kingdom
DP Dyers, based in Holmfirth, UK, has collaborated with the Future Fashion Factory on a project aimed at improving the replication of lab dyeing results in mass production, to try and reduce excessive repeat dyeing and the subsequent waste this generates.
Led by Professor Stephen Westland of University of Leeds, the Call 6 project employed the use of computational modelling to analyse inconsistencies between lab and mass dyed fabrics in order to improve results. The process has analysed the areas in which lab dyeing results do not translate to mass dyed fabrics and led to new solutions for eradicating the inconsistencies, leading to significantly reduced waste, energy and water consumption.
Continuous testing
In traditional piece dyeing, woven lengths of white fabric are dyed to a specific colour using a dye recipe. Typically, DP Dyers has been commissioned to create new shades on new fabrics with complex fibre compositions. This means continually testing dye recipes and techniques in the lab to perfect the required shade before upscaling the process for mass dyeing. In theory, anything that is produced in the lab should be able to be scaled up without any degree of error. In practice, mass dyed fabrics can show significant and varying inconsistencies compared to their lab produced counterparts. If inconsistencies do arise, the whole process must be redone.
Conditions in the lab are very tightly controlled, with variables at an absolute minimum. The lab is a fully controlled single unit and as a result is inherently better at producing and repeating results.
Machine dyeing is often performed in the opposite environment, and thus often results in discrepancies due to inconsistencies in the capabilities of the machines, complications of upscaling the dye recipe and human errors in the process, leading to a series of iterations based on trial and error.
Seamless transfer
The precision possible in the lab is therefore the only way to ensure the perfect colour match for the end fabric in a sustainable and efficient manner. Tansfer from lab to bulk production should be seamless but this has often not been possible without substantial reliance on the skill of the dyer to adjust any variation that arises in the first bulk dyeing, which is both a lengthy, resource heavy and wasteful process.
DP Dyers, part of the WT Johnson Group, has worked with Future Fashion Factory and the University of Leeds to adopt a process that has effectively digitally translated lab dye processes into mass manufacturing without the trial and error involved previously – this has consequently helped to yield significant sustainability and efficiency benefits.
The computational modelling technology – through its implementation of a matrix of complicated systems built using a variety of mechanistic approaches and complex algorithms – has helped to reduce the need for repeat dyeing. A natural consequence is therefore the reduced amount of water, chemicals and energy needed in the dyeing process, saving time and money and increasing capacity for mass production.
“This project has helped drive us on a path of improvement to be able to compete and to meet the demands of our customers,” said Alan Dolley, technical manager at DP Dyers and WT Johnson. “We cannot stand still and we use every new technology available to make improvements. For DP Dyers, the project was critical in helping the team to better understand their skills and tackle future dye rejects that can cause real problems. The potential risks can carry a need for repeat work and even result in unacceptable delays when it comes to delivery times.”
Business intelligence for the fibre, textiles and apparel industries: technologies, innovations, markets, investments, trade policy, sourcing, strategy...
Find out more