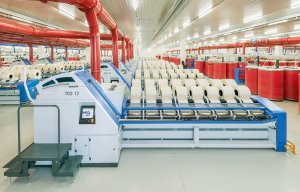
Truetzschler takes over combing business from Toyota
Latest automation updates result in ease of operation and maximum output.
28th December 2021
Innovation in Textiles
|
Mönchengladbach, Germany
The new TCO 21 comber machine from Trützschler is building on the company’s track record in spinning preparation technology to enable a boost in productivity and quality through increased automation.
One of the key benefits of the TCO 21 is its advanced processing speed. It is able to produce at a rate of up to 600 nips per minute while being coordinated with Trützschler’s highly economical Jumbo Cans, which not only reduce yarn defects due to fewer piecings, but provide significantly higher efficiency due to their larger dimensions.
The TCO 21 comes with count monitoring as standard, making it possible for the machine operator to define limits for count variations via an easy-to-use display. Trützschler’s Disc Monitor system of sensors measures the count continuously, and the machine alerts the operator and switches off if the limit is exceeded. In addition, the count monitoring function includes spectrogram analysis.
A count control function is also managed via the same easy-to-use display, and offers automatic sliver count measurement, backed up by spectrogram analysis. It automatically regulates the main draft during production to balance count variations and ensure the desired sliver count. This is particularly attractive for customers who manufacture blends of cotton and synthetics, as it can also be used to avoid variations in the overall yarn composition.
Automatic optimisation
The TCO 21 and the TCO 12 from Trützschler are the only combing machines on the market with automatic piecing optimizer technology. This identifies the right piecing setting without a single lab test, firstly by adjusting the piecing time in the combing cycle. Whereas the resetting of the detaching point (the piecing time) is usually a very time-consuming task, it now takes only a few minutes and is performed automatically at the push of a button. The operator is also assisted in selecting specific detaching curve types.
Intuitive
The Smart Touch display is fast and intuitive, and an RFID sensor quickly identifies each user and adapts the information on the display to individual needs. The multi-coloured T-LED display provides visual indications of the machine’s status or quality parameters over large distances, which enables the operator to recognise them at a glance throughout the spinning mill.
An intelligent cooling system that has already proven itself in the TD 10 draw frame contributes to a longer service life by reducing the operating temperature of electronic power components. Even if components have to be replaced at some point, the customer can keep spare parts inventory small by switching electronics spare parts flexibly between different machine types, e.g. cards and draw frames. The option to add an automatic greasing function completes the easy operation of the TCO 21.
Business intelligence for the fibre, textiles and apparel industries: technologies, innovations, markets, investments, trade policy, sourcing, strategy...
Find out more