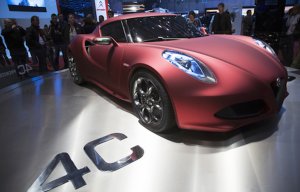
IACMI advanced composites at Detroit auto show
Special nonwovens are at the heart of a BMW initiative which may well completely change the face of the automotive industry in coming years – with lightweight, carbon fibre-based cars achieving new records in fuel consumption and performance.
23rd January 2012
Innovation in Textiles
|
Special nonwovens are at the heart of a BMW initiative which may well completely change the face of the automotive industry in coming years – with lightweight, carbon fibre-based cars achieving new records in fuel consumption and performance.
The lightweight nonwoven materials in question are being made from carbon fibres at a plant in Wackersdorf, Germany, as one step in a chain which sees them eventually converted into carbon fibre reinforced plastic (CFRP) components.
BMW observes that in contrast to woven fabrics, nonwoven bonding methods do not kink the fibres and detract from their special properties. The alignment of the fibres in the fabric is crucial to achieving optimal quality in a CFRP component.
CFRP has a wealth of benefits as a material for a car body. It is extremely corrosion-resistant and does not rust, giving it a far longer lifespan than metal. Complex corrosion protection measures are unnecessary and CFRP retains its integrity under all climatic conditions.
In its dry, resin-free state CFRP can be worked almost like a regular textile, and as such allows a high degree of flexibility in how it is shaped. The composite only gains its rigid, final form after the resin injected into the lattice has hardened.
The high tear resistance along the length of the fibres also allows CFRP components to be given a high-strength design by following their direction of loading. To this end, the fibres are arranged within the component according to their load characteristics. By overlaying the fibre alignment, components can also be strengthened against load in several different directions. As a result, the components can be given a significantly more efficient and effective design than is possible with any other material.
The ability of CFRP to absorb energy is also unique.
In April 2010 BMW announced a joint venture with SGL to build a state-of-the-art carbon fibre manufacturing plant in Moses Lake, Washington, USA. Representing an initial investment of US$100 million, this was completed on time in May 2011 and the first of two lines became operational in the third quarter of 2011.
Fibres manufactured at Moses Lake are be used exclusively for BMW’s new i3 vehicle which is set to be launched before 2015 under a BMW sub-brand and will be assembled in Leipzig, Germany.
“The selection of CFRP on this scale for a volume-produced vehicle is unprecedented, because it has previously been thought of as too expensive and still not sufficiently flexible to work with and produce,” says Hanno Pfitzer, who works in process development for BMW at Landshut in Germany, where the nonwoven fabrics will be turned into CFRP parts and components.
“The extensive use of CFRP makes modules extremely light and gives the car both a longer range and improved performance. In addition, it has clear benefits in terms of the car’s handling – the stiffness of the material makes the driving experience more direct, with even rapid steering movements executed with flawless precision. At the same time, CFRP enables a higher level of ride comfort, because the stiff body dampens energy inputs extremely effectively. As a result, unwanted vibrations are eliminated.”
The BMW Group’s CFRP strategy also extends beyond the life cycle of the product and it has developed a concept for recycling segregated production waste into commercial-quality raw material. This system allows a substantial proportion of carbon fibre waste to be returned to the production process. Thanks to a special refining procedure, the resulting material can even be used as a substitute for primary fabric.
“Using CFRP is more than simply a straight substitution, like using aluminium in place of steel,” Mr Pfitzer said.
“With its special properties, this material also opens the door to completely new approaches and design concepts. Provided that this material is properly understood, it can be strategically deployed to achieve vast improvements in a wide range of lightweight products.”
Visitors to INDEX14 will be able to gain first-hand knowledge of the many nonwoven products currently benefiting the automotive industry.
This article originally appeared in the INDEX14 Newsletter and has been republished with the kind permission of EDANA.
Business intelligence for the fibre, textiles and apparel industries: technologies, innovations, markets, investments, trade policy, sourcing, strategy...
Find out more