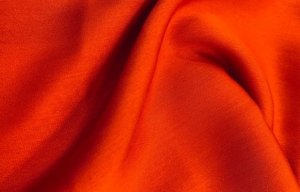
Teijin develops easy-care silk-like polyester fabric
The millennia old tradition of silk production is about to be woven into the fabric of the 21st century. Under the ‘Tango Biofabrics’ project, Japan's Teijin is attempting to develop new, eco-friendly applications for Biofront, a type of bioplastic, in collaboration with Kyotango, a city long known as the home of Tango silk crepe, or chirimen. Teijin hopes to combine its advanced heat-resistant bio plastic fibres with Kyotango’s traditional silk craftsmanship fo
25th January 2010
Innovation in Textiles
|
Osaka
The millennia old tradition of silk production is about to be woven into the fabric of the 21st century. Under the ‘Tango Biofabrics’ project, Japan's Teijin is attempting to develop new, eco-friendly applications for Biofront, a type of bioplastic, in collaboration with Kyotango, a city long known as the home of Tango silk crepe, or chirimen.
Teijin hopes to combine its advanced heat-resistant bio plastic fibres with Kyotango’s traditional silk craftsmanship for innovative applications that leverage Biofront’s silk-like sheen, as well as its durability and heat resistance, which Teijin says is superior to conventional bioplastic fibres.
Kyotango, which is located near Japan’s ancient former capital of Kyoto, hopes that the project will stimulate new business in its traditional silk industry, enabling local companies to apply their expertise in creative new ways using Biofront fibres. Several silk production and processing companies are now partnering with Teijin toward this end.
Teijin says conventional bioplastics such as polylactide have limited applications because of their lower heat resistance, generally about 170 degrees C, as well as less durability than petroleum-derived plastics. Biofront, however, has a melting point of 210 degrees C, which is comparable to petroleum-derived PBT (polybutylene terephthalate). Biofront is resilient enough to withstand ironing, while other Biofront products can endure high-temperature processing such as plastic moulding and fabric dyeing.
Teijin also claims that Biofront also overcomes conventional bioplastic’s problems with hydrolytic degradation in high heat and humidity, thanks to Teijin technology that controls reactions at the molecular level. The result, the company says, is a material as durable as PET (polyethylene terephthalate), but without any loss of heat resistance, providing a promising alternative to widely used PET and PBT.
On top of these advantages, Teijin expects to develop Biofront as a highly impact-resistant, antibacterial and flame-retardant material for moulding processes.
Teijin has been steadily developing and refining applications since launching Biofront in 2007. The list includes car seat fabric co-developed with Mazda, automotive front panels, clothing materials and eyeglasses frames. Exciting applications envisioned in the coming future include automotive and electronics components capable of withstanding especially harsh conditions.
Last September, Teijin launched a Biofront demonstration plant with an annual capacity of 1,000 tons, bringing the business closer to full-scale operation. The aim is to establish a mass production system with a 5,000-ton capacity by 2011.
Business intelligence for the fibre, textiles and apparel industries: technologies, innovations, markets, investments, trade policy, sourcing, strategy...
Find out more