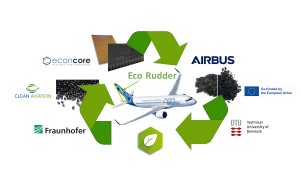
Sustainable rudder for Airbus A320
With the Ultrason E, manufacturers can now take a great step forward in making sandwich structures for airplane interiors cost effectively and quickly.
14th August 2018
Innovation in Textiles
|
Ludwigshafen
The sandwich consists of a foam core and carbon fibre laminates, which are all made of Ultrason E. If needed, the thermoformed foam core with cover layers can then be overmoulded with the carbon-fibre reinforced Ultrason E 2010 C6 to incorporate reinforcements, structures or additional functional elements into the sandwich. The combination of 30% carbon fibres with the amorphous high-temperature plastic Ultrason is said to guarantee extraordinary and constant mechanical properties for the light foam sandwich over a temperature range of -100 to +200°C.
Business intelligence for the fibre, textiles and apparel industries: technologies, innovations, markets, investments, trade policy, sourcing, strategy...
Find out more