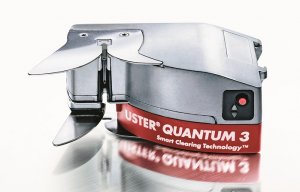
Stopping poor quality at source with Usterquantum 3
Uster ring spinning optimisation system now offers much more than end-break detection, the company reports.
5th September 2018
Innovation in Textiles
|
Uster
Uster Technologies, a leading high-technology instrument manufacturer, is introducing its Uster Sentinel, a comprehensive solution for ring spinning optimisation, with benefits in quality, productivity and efficiency, according to the company.
“Data can now be integrated with the Total Testing Center through Uster Tester 6, giving spinners an overview of quality through all process steps in the mill, for focused control of production management. Adding Uster Roving Stop enhances the economic advantages still further, reducing waste by stopping the roving feed immediately an end-break is detected,” it explains.
Uster Sentinel’s bobbin build-up report is the key to optimised yarn production. The system’s detection of end-breaks provides the basic platform, which is extended to total control of end-breaks when combined with Uster Roving Stop. The instant stop of roving feed at an end-break will reduce waste significantly and make raw material usage more cost-effective. Calculations show that 70% less pneumafil waste equates to a saving of nearly 1% in raw material, based on current spinning conditions. “This obviously makes for a shorter investment payback,” the company continues.
Using Uster Sentinel with Uster Roving Stop is designed to improve productivity and cut down the risk of quality problems in ring spinning. Potential quality claims are avoided, since waste material and uncontrolled fibre – which could affect neighboring spindles and the entire machine – are greatly reduced by the Uster Roving Stop.
Overload on rollers is also prevented, ensuring higher productivity through reduced lapping. These benefits together can be expected to extend the service life of spinning components such as aprons, cots and cylinders by around 20%, according to the manufacturer.
According to Uster, the new Uster Sentinel brings a new approach to quality, productivity and efficiency in ring spinning. Bobbin build-up information and end-break detection are the basic functions, but total optimisation is the result. The intuitive reports on bobbin build-up include every parameter influencing end-breaks. Clear visuals point to exact reasons for breaks, making optimisation easy.
Machine performance is displayed in real-time, giving a fast overview of the most relevant production and laboratory data – as well as the machine’s energy consumption. The well-established expert system supports mills with clear guidance to profitable optimisation.
“Uster’s ring spinning optimisation system maximises profitability where it matters most. Uster Sentinel measures and controls the most expensive process in yarn manufacturing. It monitors the productivity of all spindles, as well as providing the required links and information to help the spinning mill optimise both machine performance and the entire process,” the company says.
“Connecting Uster Sentinel to the Total Testing Center of the Uster Tester 6 opens the way to extended analysis, based on centralised quality data from all spinning processes. This is the route to management of a spinning mill with quality in mind. Adding Uster Sentinel data to this creates the ultimate quality optimisation package. This is a significant further development milestone, supporting spinners to achieve the ultimate goal of excellence in quality and profitability.”
Business intelligence for the fibre, textiles and apparel industries: technologies, innovations, markets, investments, trade policy, sourcing, strategy...
Find out more