ASCC’s big ideas boosted by Optima 3D weaving
Composites
3D printer breaks Guinness World Record
Initiatives will include the development of biobased feedstocks for BioHome3D.
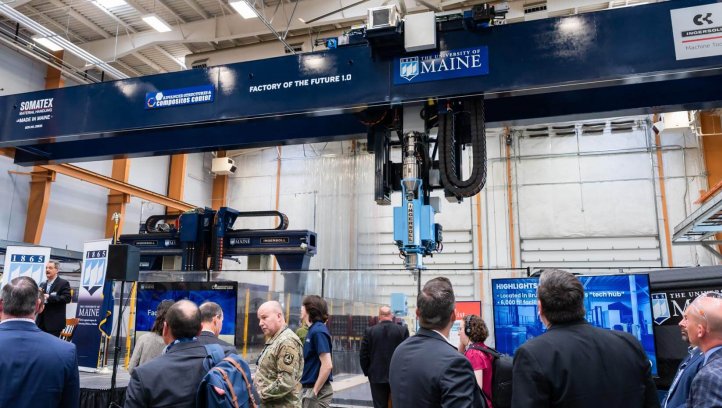
7th May 2024
Innovation in Textiles
|
Maine, USA
Surpassing its own record for the largest polymer 3D printer, University of Maine (UMaine) has unveiled a next-generation printer at its Advanced Structures and Composites Center (ASCC) that is four times larger than its predecessor.
The thermoplastic polymer printer, dubbed Factory of the Future 1.0 (FoF 1.0), is designed to print objects as large as 30 metres long, ten metres wide and 5.5 metres high, and can print up to 227kg per hour. It offers new opportunities for eco-friendly and cost-effective manufacturing for numerous industries, including national security, affordable housing, bridge construction, ocean and wind energy technologies and maritime vessel fabrication. The design and fabrication of the printer and hybrid manufacturing system was made possible with support from the US Office of the Secretary of Defense through theArmy Corps of Engineers.
FoF 1.0 isn’t merely a large-scale printer – it dynamically switches between various processes such as large-scale additive manufacturing, subtractive manufacturing, continuous tape lay-up and robotic arm operations. Access to it and MasterPrint, the ASCC’s first world-record breaking 3D printer, will streamline manufacturing innovation research at the centre and the two large printers can collaborate together.
“UMaine and the Advanced Structures and Composites Center possess the innovation, capacity and workforce to support the future needs of the Department of Defense in advanced manufacturing,” said US senator Susan Collins, who has secured more than $93 million in support of the initiative and other defense projects at the ASCC.
“FoF 1.0 opens up new research frontiers to integrate these collaborative robotics operations at a very large scale with new sensors, high-performance computing and artificial intelligence to create born-certified systems that meet high quality standards,” said ASCC executive director Habib Dagher. “We are grateful for Senator Collins’ support, for support from Maine’s congressional delegation and for collaborations with the Department of Defense, Department of Energy, Oak Ridge National Labs, Maine Housing and our industry partners here in Maine and beyond.”
Wood residuals
The one-of-a-kind printer will advance various initiatives, including the development of biobased feedstocks from wood residuals abundant in Maine. It will advance commercialisation efforts such as BioHome3D and the creation of sustainable, affordable housing, while also propelling crucial technological advancements for national security, particularly in lightweight rapidly deployable structures and vessel technologies.
“The Department of Defense has been advancing composites and manufacturing technologies with the University of Maine ASCC for nearly two decades,” said Heidi Shyu, undersecretary of defense for research and engineering and chief technology officer for the Department of Defense. “The latest innovations in manufacturing, composite technologies and materials coming from our universities will continue to be instrumental to the security and economic vitality of the USA and its allies and partners worldwide.”
The FoF 1.0 unveiling comes ahead of this summer’s planned groundbreaking of a new 47,000-square-foot research laboratory called the Green Engineering and Materials (GEM) Factory of the Future scheduled for August. Its primary aim is to facilitate and scale up more sustainable manufacturing practices by introducing next-generation solutions and biomaterials, addressing challenges such as a diminishing workforce and strained supply chains with local solutions.
“Maine needs an estimated 80,000 additional homes by 2030, many specifically for households with incomes at or below the area median income,” said MaineHousing’s development director Mark Wiesendanger. “This new technology allows UMaine-ASCC to scale-up its research and production of its biobased 3D printed home technology.”
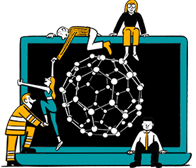
Business intelligence for the fibre, textiles and apparel industries: technologies, innovations, markets, investments, trade policy, sourcing, strategy...
Find out more