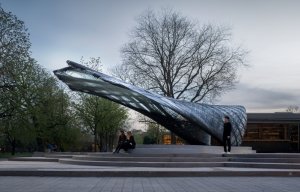
Apple leaf miner inspires new processes for composite construction
Opinion
It seems apt that the week in which the highly successful Composites Engineering show was held at the NEC in Birmingham, UK, culminated in the first BMW i3 electric cars being handed over to their first purchasers over in Munich in Germany. Because the composites industry is currently in love with carbon.
17th November 2013
Adrian Wilson
|
Munich
It seems apt that the week in which the highly successful Composites Engineering show was held at the NEC in Birmingham, UK, culminated in the first BMW i3 electric cars being handed over to their first purchasers over in Munich in Germany.
Because the composites industry is currently in love with carbon.
There can be few who are not familiar with the BMW i3 story by now, but it remains an inspiring one because of the German car manufacturer’s absolute conviction that electric vehicles will move into the mainstream very shortly, and that carbon fibres and fabrics as the basis of composite car bodies will also soon become the norm.
And BMW is intent on leading the field in both respects. It has invested a huge amount into establishing infrastructure and networks in both the USA and Germany that will start from the raw materials through to the i3 electric cars rolling off the production line. It’s also employed hundreds of new development engineers and has thought the project through to the extent that even the very first i3 vehicles being sold this week, already come with certification that their greenhouse gas emissions potential is between 30-50% less than conventional cars of their size and performance.
All of the waste from the i3 plants, meanwhile, is being recycled into nonwoven fabrics, some of which are even appearing in the roof of these first i3 vehicles.
BMW had solid grounds for this initiative, of course.
In the aerospace industry, the use of carbon fibre as the basis for composite parts has already grown from representing 10% of a plane’s body twenty years ago to over 50% in today’s superplanes – the Airbus A380 and Boeing’s Dreamliner. In addition, military forces worldwide are using more carbon fibre than ever before in their aircraft and many other items of equipment.
The benefits carbon fibre composites bring are multiple, but vitally, result in a considerable weight reduction in replacing steel. It’s all about fuel consumption, calculated over the lifetime of a plane and in the context of the operator’s full fleet.
The other advantages of carbon fibre composites for vehicles include the design flexibility they make possible as a result of the reduced number of parts and even enhanced aesthetics. The lifetime of a vehicle is also improved due to the fatigue and corrosion resistance of the materials.
Poor old glass fibre, meanwhile, has been the staple for the composites industry for at least thirty years – and still comprises around 80% of all composites produced today.
But it simply lacks the glamour and the sexiness. Why showcase a highly functional gas tank, for example, when you can turn heads with a Formula 1 racing car chassis instead?
And there’s even worse news for glass fibre as a result of all the carbon fibre composites development work that’s now going on.
At the Composites Engineering show, the UK wetlaid nonwovens specialist Technical Fibre Products (TFP), announced that it is now successfully recycling carbon fibre composites into high value nonwovens.
Via a process called fluidised bed recovery, carbon fibre composites that have reached end-of-life are being recycled into mats that can successfully replace previously glass-based alternatives – and are being sold back to the aerospace majors who supply the carbon composite waste in the first place.
So far, recycling carbon composites has involved pyrolysis – in which waste material is placed in high-temperature furnaces to recover the fibres, while sacrificing the resin, which can comprise up to 50% of the part.
Even this is now being addressed, however.
At the Birmingham event this week, Bo Liang, chairman and CEO of Adesso – a US-invested company headquartered in Wuxi, China, which this year has opened an R&D centre in Cambridge, UK – introduced recyclable epoxy resins for the production of sustainable carbon fibre composites.
Adesso has developed two products – Cleavamine degradable curing agents and Recycloset recyclable epoxies – which allow the chemical recycling of carbon fibre components at atmospheric pressure and temperatures below 150°C.
“This a simple and clean process that’s not reliant on high temperature or harmful waste streams,” Liang said. “The fibres are suitable to be reused as structural reinforcements while the resins can serve as toughening agents in adhesives and moulding compounds.”
But one problem remains.
It’s been estimated that for the production of around 1,000 planes a year, the total amount of carbon fibre required is 50,000 tons, based on an average of 50 tons going into each plane.
Even if just 100kg of carbon fibre composites were to be employed in the annual 100 million cars being built each year, the demand would be 10 million tons.
That’s 1.5 million tons more than the total global production of carbon fibre which will be available in 2015 after current planned capacity expansions.
Business intelligence for the fibre, textiles and apparel industries: technologies, innovations, markets, investments, trade policy, sourcing, strategy...
Find out more