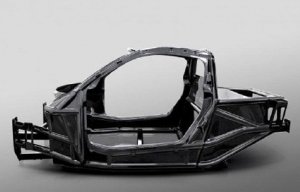
Stacking based on continuous carbon fibre tow
The Elytra Filament Pavilion has been constructed on-site and is the work of German architect Achim Menges and structural engineer Jan Knippers.
22nd July 2016
Innovation in Textiles
|
UK
The forewing shells of the flying elytra beetle have inspired a new carbon and glass fibre-based architectural installation outside London’s Victoria and Albert Museum (V&A).
The Elytra Filament Pavilion has been constructed on-site robotically and is the work of German architect Achim Menges and structural engineer Jan Knippers, the leaders of research institutes at the University of Stuttgart in Germany. Their teams are pioneering the integration of biomimicry, robotic fabrication and new materials research in architecture and this is their first-ever major commission in the UK.
Each component of the undulating canopy is produced using a robotic winding technique developed by the designers. Like the elytra beetle, the pavilion’s filament structure is both very strong and very light – spanning over 200 square metres, it weighs less than 2.5 tonnes.
Elytra is a responsive shelter that will grow over the course of the V&A’s Engineering Season which runs until November. Sensors in the canopy fibres will collect data on how visitors inhabit the pavilion and monitor the structure’s behaviour, ultimately informing how and where the canopy grows. During a series of special events as part of the V&A’s Engineering Season, visitors will have the opportunity to witness the pavilion’s construction live, as new components are fabricated on-site by a KR 120 R2500 robot from the KR Quantec range manufactured by Kuka Roboter, of Augsburg, Germany.
Germany’s SGL Group supplied its Sigrafil 50k carbon fibres for the installation and assisted the project team with material expertise and advice.
“The installation impressively demonstrates the wide-ranging potential for innovative application of composite materials,” said Andreas Wüllner, head of SGL’s Composites Fibres and Materials business unit. “It also shows the high degree of automation that is now possible in the industrial production of components from composites.”
SGL’s Sigrafil 50k fibres are especially suitable for automated production processes. Among other applications, the fibres are used as standard in the BMW i3, i8, and new 7 series, produced at the world’s largest and most modern carbon fibre plant at Moses Lake in Washington.
Business intelligence for the fibre, textiles and apparel industries: technologies, innovations, markets, investments, trade policy, sourcing, strategy...
Find out more