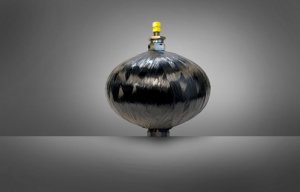
First recycled COPV from Steelhead
Material of particular interest for high temperature applications of up to 2000°C.
16th May 2023
Innovation in Textiles
|
Sheffield, United Kingdom
A prototype machine developed within the UK-based CICSiC project enables the mechanical properties of silicon carbide (SiC) in ceramic matrix composites (CMCs) to be more closely specified to enhance aerospace applications.
The project brought the University of Sheffield Advanced Manufacturing Research Centre (AMRC) together with companies Archer Technicoat (ATL), TISICS Metal Composites and Cygnet Texkimp to focus on the manufacturing routes for SiC CMCs as a material of particular interest for high temperature applications of up to 2,000°C, in sectors such as aerospace, space and nuclear.
“SiC-based ceramic matrix composites are a promising material for many extreme environment applications including aircraft engines,” explained Ryan Skillett, technical manager at ATL. “The CICSiC project has kick-started the development of a new method for manufacturing these high value materials aiming to simultaneously bring down costs while improving performance and reliability.”
Reel-to-reel
The new reel-to-reel coating process can replace the current batch coating method to apply interphase coatings to CMCs. In the batch coating method, a preform is made from uncoated fibre which is treated in one step, making it difficult to ensure an even coverage of all areas of the preform with equal precision. The new method uses a reel-to-reel process to apply the interphase coating. The material is wound from its original spool onto a new spool with the interphase being applied inbetween, to ensure uniform coating. Because the material is still on a spool, it can easily be used in fibre processing technologies, allowing for shapes with increased complexity to be formed with a uniform interphase coating.
“The project worked towards the creation of a continuous fibre coating system to work in harmony with the existing batch-based technology, in order to take on some of the major barriers to market for the product,” Skillett explained. “The results of this project have drawn international interest from specialists in the material, leading us to believe it has a very bright future.”
Industrial scale
The AMRC’s role in the project focused on the industrial scale processing of SiC fibres to produce preforms with increased complexity. The ability to process the fibres is key to realising the potential of the material. Utilising SiC fibres in processing technologies such as weaving and tailored fibre placement (TFP) is important for building confidence in the handling of these materials and understanding the current processing limits.
The work on handling fibres was performed on SiC provided by ATL that had undergone the coating procedure in order to understand the difference in processing requirements, limitations and the quality of the output.
“Silicon carbide composites are of interest to many industry sectors looking at high temperature applications,” said Steffan Lea, a technical fellow in the AMRC’s composites team. “The ability to produce more complex preforms from continuous silicon carbide fibre will enable new designs and applications for this high performance ceramic matrix composite material.
“During the project, the AMRC has gained familiarity and knowledge on how to process SiC fibres on industrial-scale machines. Our knowledge on how to process the fibres on weaving looms to produce 3D woven preforms enables the production of unitised preforms with added complexity. Using TFP allows us to make efficient use of the material, only placing it where it is required and controlling the path of the fibre to make best use of its properties.”
“Working on this project has allowed us to understand the challenges associated with handling very delicate ceramic fibres,” added Andy Whitham, director of process development at Cygnet Texkimp. “These are unusual in some of their characteristics, so having first hand experience of the difficulties involved in their use is invaluable. Beyond that, the opportunity to work with new partners from outside Cygnet Texkimp’s main sectors always provides a different view on the machinery we might supply for a given application.”
Business intelligence for the fibre, textiles and apparel industries: technologies, innovations, markets, investments, trade policy, sourcing, strategy...
Find out more