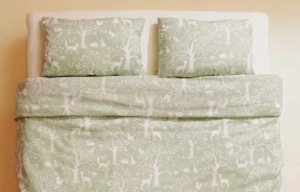
IKEA joins the CanopyStyle initiative
Hybrid yarns of cotton and PLA selected for knitted covers.
6th December 2021
Innovation in Textiles
|
Germany
Biodegradable yarns for use in reforestation project growth covers have been developed by the German Institutes of Textile and Fibre Research Denkendorf (DITF).
Growth covers prevent game from feeding on the young plants and help to ensure they are not prevented from growing by other plants, according to Stephan Baz, Head of Staple Fibre Technologies at DITF.
Covers available on the market made of plastic and metal should be removed and collected after three to five years, but this often doesn’t happen, or is no longer possible due to overgrowth or because the cover has grown into the tree. As a result, numerous growth covers remain in German forests every year until they rust or are shredded into environmentally-harmful plastic components by external influences. Although currently available variants made of bioplastics are based on renewable raw materials, they are not biodegradable, decompose during the use phase and pollute nature with small and microplastics.
Buck GmbH, based in Bondorf, Germany, therefore commissioned the DITF to develop a yarn from renewable raw materials that is also biodegradable. The yarn has to be able to be turned into a stiff but at the same time pliable tube on a knitting machine.
Fibres
Renewable natural fibres and polylactide (PLA), which Trevira provided free of charge for the research, were used as starting materials for the development of the hybrid yarn. PLA consists of chemically bonded lactic acid molecules and is currently the only biodegradable thermoplastic available on an industrial scale. Particular attention was paid to ensuring that the PLA was pure in order to avoid environmental damage from plasticizers or other ingredients.
Flax fibres were initially used as renewable natural fibres. In several successive processes of spinning preparation, they were opened with the PLA staple fibres, mixed and processed into a fibre sliver. A simple, widely used spinning process had to be employed to ensure rapid implementation on an industrial scale. Spinning trials were carried out on a rotor spinning machine, on a roving frame, and on a spiral covering spinning tester developed at the DITF.
Roving productionon the roving frame was finally selected, since it produces a voluminous and strong hybrid yarn with sufficiently flexible setting parameters and, moreover, is widely used by many spinning mills. The hybrid yarn was then processed at Buck GmbH into a knitted fabric from which the beam covers were made.
The flax fibres were then replaced by cotton to optimise the hybrid yarn, since cotton is more flexible across the longitudinal fibre axis.
Business intelligence for the fibre, textiles and apparel industries: technologies, innovations, markets, investments, trade policy, sourcing, strategy...
Find out more