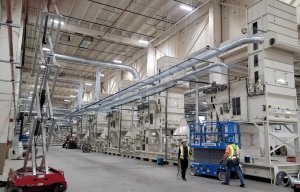
Large-scale hemp gin up and running in Texas
Opinion
Helping garments look and feel new for longer could have a major impact.
7th November 2022
Adrian Wilson
|
Bagsvaerd, Denmark
Novozymes, the leading manufacturer of enzymes and microbes that improve industrial manufacturing, sets great store in R&D – a commitment underlined by the fact that the company’s 6,000 employees are eclipsed by its 6,500 patents.
Speaking at the WTIN Innovate Zero Carbon conference (November 1-3), the company’s global marketing manager Dina Lipp outlined the significant benefits its enzymes can make in various stages of textile wet processing.
The enzymatic desizing of knitted fabrics, for example, can eliminate as much as 700kg of the chemicals usually required – including sodium hydroxide and hydrogen peroxide – in the production of a one ton batch.
Several stages of wet processing, for example bioscouring, enzymatic bleach clean up and biopolishing, can also be combined in a one-step process to save 350kg of CO2 and 13 m3 of water per ton of fabric.
In the bigger picture, over the year 2019, Novozymes has calculated that its solutions helped the textile industry to save:
- 37 million Gj of energy – corresponding to six million barrels of oil.
- 2.6 million tons of CO2 – equating to taking a million cars off the road.
- 83 million m3 of water – 33,000 Olympic swimming pools.
- Two million tons of chemicals, corresponding to 70,000 truckloads.
Extending life
Another significant area in which biotechnology can help the industry is in extending the active lifetime of garments, which it has been calculated can reduce overall climate impact by up to 49%.
“Biopolishing has been proven to help garments look and feel new for 20% longer, which is more significant than it might sound,” said Lipp. “As we all know, it takes considerable amounts of water, energy, chemicals and fibres to make a simple t-shirt and when it reaches the consumer it will be used on average 30 times and washed maybe 15 times. If it was used 60 times instead, its climate impact would be cut in half.
“Our latest consumer research has shown that over 70% of buyers are annoyed with fuzz and pilling on garments after washing and in many cases t-shirts are often discarded early as a result. This is where biopolishing makes a huge difference. The treatment gives a durable fuzz and pill-free surface, retaining a softer hand feel and keeping colours bright for at least 20% longer.”
If all cotton t-shirts in the world were used for 20% longer, she added, the industry could save an annual 24 million tons of CO2 emissions and 27 billion m3 of water – more than the consumption of the US, Canada and Mexico.
The contribution of garment durability was a key theme during the Innovate Zero Carbon conference.
Novozymes has recently taken biopolishing beyond cotton with a new solution for manmade cellulose, extending its benefits to viscose, lyocell and modal-based fabrics.
“A garment’s active life is a key factor in determining its climate impact,” Lipp concluded. “ We should not just produce with less resources or try to optimise production processes, which of course are both very important but are not enough. For fashion to become more circular we must also promote sustainable design and long-lasting quality.”
Business intelligence for the fibre, textiles and apparel industries: technologies, innovations, markets, investments, trade policy, sourcing, strategy...
Find out more