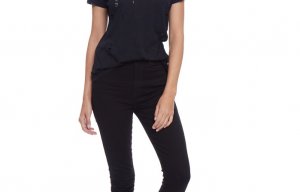
Cone Denim launches Future Black+ denim
Many exhibitors within this Intertextile Shanghai will be showcasing their efforts to drive the industry towards a more eco-friendly future.
31st July 2017
Innovation in Textiles
|
Shanghai
With the pace of change in the textiles industry seeming to increase at an ever-faster rate, it is becoming more and more important to stay ahead of the curve, say organisers of Intertextile Shanghai Apparel Fabrics. This October, the show plays host to some of the industry’s leading innovators, including DuPont, Eastman Chemical, FENC, Hyosung, Invista, Lenzing, Nilit, The Chemours Company, Toray and Unifi.
A number of exhibitors within this edition’s Beyond Denim will be showcasing their proprietary efforts to drive the industry towards a more eco-friendly future, including Turkey’s Orta Anadolu and Kipas Denim, and Soorty Enterprises from Pakistan. The larger Beyond Denim this year will include around 190 overseas and Chinese exhibitors, as well as an Invista Pavilion and Forum highlighting exhibitors’ products.
Orta Anadolu will showcase its AW 18/19 collection under the theme Jeans Matter. “Denim has and always will have a special handprint on culture. In times of social change, Jeans Matter,” the company explained. Orta has launched a new concept it calls Indigo Flow which combines the Reserve Flow and Clean Flow processes for a more eco-friendly indigo dyeing process. Reserve Flow can reduce water usage by up to 70% through savings at the water feeding and finishing stages, while energy is saved by not requiring heat during the fixing process. The Clean Flow process is unique to Orta as it utilises an organic reducing agent which is said to lead to cleaner waste water, no salt formation and less chemical usage.
Like Orta, Kipas Denim has developed its own technology to address the shortcomings during denim fabric production. The Conservablue technology aims to reduce the environmental impact of the dyeing process. Conventionally made jeans pass through six rinsing overflow boxes before and after the indigo dye boxes, which Conservablue eliminates altogether leading to water, waste water, electricity and dyestuff savings.
As with Kipas Denim, Soorty Enterprises emphasises its eco-friendly efforts along the entire production chain, from cotton sourcing to finishing. The company’s new Zero Water Blue concept promises water savings of up to 90% by eliminating water usage at the rope dyeing stage, and reducing it at the finishing stage by merging the traditional de-sizing and mercerisation steps into one ‘relaxing’ step. “This new step, along with eliminating water usage at the final sanforisation stage, not only saves water overall but also eliminates caustic and acid use during this stage as well,” the company reports.
For the first time Intertextile Shanghai will also play host to one of the industry’s leading innovators – Shima Seiki, of Wakayama, Japan. With over 2,000 worldwide patents and patents pending, and 30 years of research experience in knitting technology, the computerised knitting machine manufacturer will exhibit at the fair alongside a number of its partners including yarn suppliers and knitwear manufacturers, providing a one-stop knitwear solution under the theme Future Knitwear.
Shima Seiki is well known for its Wholegarment manufacturing technology – where an entire knitted garment is produced on the knitting machine without the need for linking or sewing afterward – but it will be its SDS-ONE APEX3 3D design system, the latest version of which will be on display at Intertextile Shanghai, which makes this theme highly appropriate, organisers explain.
The system integrates production into one workflow, from yarn development, product planning and design to production and even sales promotion. One key feature is its Virtual Sampling function, which is designed to improve the design and evaluation process, and minimise the time, cost and material usage during the sample-making process. The overall effect of this system can be to shorten the production cycle to such an extent that mass-customisation of garments can be achieved.
Business intelligence for the fibre, textiles and apparel industries: technologies, innovations, markets, investments, trade policy, sourcing, strategy...
Find out more