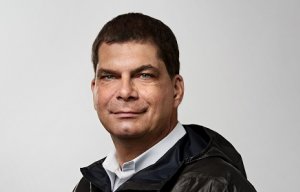
Gore Fabrics reports latest progress in sustainability
Gore Fabrics increases use of recycled and solution-dyed textiles in garments portfolio to contribute to water savings and reduced CO2 emissions.
14th June 2018
Innovation in Textiles
|
Feldkirchen-Westerham
At its booth, from 17-20 June, Gore will present a range of Gore-Tex 2-Layer jackets, manufactured by customers like Berghaus, Haglöfs and Marmot, amongst others, that utilise – for the first time – a DWR (Durable Water Repellent) treatment free of PFCEC.
In addition, the outdoor jackets shown at the booth reflect a second big step forward in Gore Fabrics´ efforts to reduce the environmental footprint of its products, the company reports. All the products are manufactured with Gore laminates utilising face-textiles made from recycled materials – another key initiative within Gore Fabrics´ strategy.
Using recycled materials helps reduce the amount of plastic waste that otherwise would end up in landfills or incineration, according to the manufacturer. Gore’s recycled nylon is currently sourced from pre-consumer waste while its recycled polyester stems from used PET bottles.
“The Gore-Tex jackets shown at our booth have a PFCEC-free DWR treatment and face-textiles made from recycled materials. They represent the strong intent of both us and our customers to offer environmentally improved products,” said Bernhard Kiehl, Gore Fabrics´ Sustainability Leader. “The positive feedback we have received on our innovations motivates us to work even harder on developing further advanced material solutions. We continue our efforts to deliver fit-for-use products that provide the ideal combination of high performance, durability and a low environmental footprint.”
While Gore Fabrics´ current product collection for the Autumn/Winter 2018 season offers more than a dozen Gore-Tex laminates that are manufactured with face-textiles made from recycled materials, this number is expected to almost triple by A/W 2019. This will correspond to approximately 10% of Gore Fabrics´ total consumer laminate offering.
Also, ready to be rolled-out by customers for the A/W 2019 season is another innovation: solution-dyed face-textiles, which will add alternative consumer laminate options to the Gore-Tex collection for A/W 2019. Solution dyeing is a yarn-dyeing technology that – compared to conventional dyeing processes – saves up to 60% in water usage and significantly reduces CO2 emissions, according to the company. During the solution-dyeing process, dyestuffs are mixed with the nylon or polyester pellets prior to spinning into yarn. The resulting yarn is permanently, deeply coloured and ready to be woven into fabrics.
Gore Fabrics has also developed a new textile backer that combines the advantages of solution dyeing and recycled content, resulting in an attractive offering of an additional range of 18 laminates with solution dyed content to Gore -Tex brand partners from 2019 onwards.
“We seek to expand our share of solution-dyed textiles due to two compelling advantages: solution-dyeing helps reduce our environmental footprint, and it offers a performance benefit of superior colour-fastness, which will allow consumers to enjoy brilliantly bright colours for longer than usual. And, as we know from our Life Cycle Assessment studies, using durable outerwear for a long time is the best thing you can do reduce its impact on the environment,” explained Thomas Kiebler, Gore Fabrics’ Application Engineer Leader.
Business intelligence for the fibre, textiles and apparel industries: technologies, innovations, markets, investments, trade policy, sourcing, strategy...
Find out more