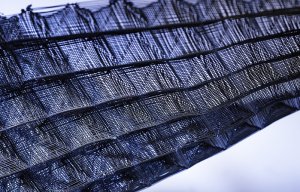
Monforts to debut its texCOAT coating range at Techtextil 2017
Monforts reports increasing success with its latest fully integrated Montex Coat finishing lines.
18th May 2020
Innovation in Textiles
|
Mönchengladbach
A typical integrated Monforts coating line is automated from the inlet feed to the winder.
Monforts reports increasing success with its latest fully integrated Montex Coat finishing lines.
A typical integrated Monforts coating line is automated from the inlet feed to the winder and includes weft straightening, the Montex Coat coating device, Montex TwinAir drying chambers, an Eco Booster heat recovery system and a cooling zone, with visual touchscreen control via the proven Qualitex system and full Teleservice access and as well as a new hand-held device.
A number of doctor blade options are available for the Montex Coat coating unit, including air knife, roller knife, magnetic roller and foam coating, in addition to screen printing. The company also provides fully explosion-proof lines for solvent-based coatings and for high-temperature processes up to 320°C, such as for PTFE sintering.
Wide widths
There has been a notable adoption of magnetic roller coating technology, the company, which is headquartered in Mönchengladbach, Germany, notes – especially by technical textiles and nonwovens manufacturers who are finishing wide-width materials.
With this option, it is possible to carry out applications such as full PVC coatings, pigment dyeing or minimal application surface and low penetration treatments.
The Montex Coat unit available for customer trials at the Monforts Advanced Technology Centre in Mönchengladbach, Germany.
Typical products this technology is eminently suited to, range from tents and awnings, black-out roller blinds and sail cloth to automotive interior fabrics and medical disposables.
“Magnetic roller coating allows a wide range of coatings and finishes to be carried out, while being easy to handle for operators and much easier to clean at the end of the process,” explains Jürgen Hanel, Monforts Head of Technical Textiles. “As important as anything, however, is the coating uniformity it guarantees, with no difference in tension across the entire width of the fabric – which is particularly important when companies are operating at wide widths.”
“With traditional dip coating systems,” he adds, “as well as with many standard knife coating technologies, there is always a difference in the tension – and hence the amount of pressure with which the coating is applied – between the centre and the edges of the wide width fabrics being treated. With the use of a magnetic roller, there is no difference in the pressure being applied anywhere on the fabric.”
“Our magnetic roller technology provides textile finishers with an expanded range of options due to the fully-adjustable positioning of the magnet within the roller,” explains Hanel. “With four different magnet positions possible, the roller can be set to operate both as a direct coating system and as an indirect coater. We recommend the use of this technology for companies working with fabrics of over 2.4 metres.”
“Adjusting the roller surface, rather than changing the finishing formulation, to match the required add-on and viscosity for each coating effect required, leads to much higher output from the line,” he adds.
Hand-held control
Furthermore, adjustments can now be made simply and easily with the new hand-held remote controller which has recently been introduced for the Montex Coat unit.
Adjustments can be made simply and easily with the new hand-held remote controller which has recently been introduced for the Montex Coat unit.
“This is a really big help because making adjustments manually was previously quite time consuming and operators had to move between the fixed control panel and the position of the adjustment constantly,” Henel says. “It also allows an operator to check that the knife is precisely positioned by simply holding the device in the position where he or she can see and measure the gap. With the device the motors can be controlled, and the necessary adjustments carried out.”
Also offered as an option for the Montex Coat is a carbon fibre roller for meeting even the highest level of coating accuracy that is being demanded by the most exacting customers today.
This provides the extreme stiffness necessary to deal with the winding tension required in the processing of materials such as prepregs for composites and other heavyweight fabrics, but at the same time, a significant improvement in coating accuracy is achieved, even for very lightweight flexible materials. In addition, the surfaces of the rollers are protected against both abrasion and damage from aggressive chemicals by a special ceramic coating.
“We continue to focus on incremental improvements to our technologies to better serve our customers - and with our Montex Coat we have a most versatile product in our portfolio.” said Monforts vice-president Klaus Heinrichs.
Business intelligence for the fibre, textiles and apparel industries: technologies, innovations, markets, investments, trade policy, sourcing, strategy...
Find out more