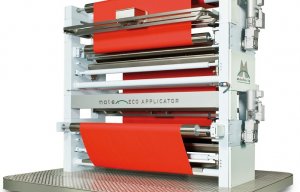
Rapid success for Eco Applicator
The installation is part of a programme that has seen over 25 million Swiss francs invested in new technology at the Schoeller plant over the past decade.
8th October 2018
Innovation in Textiles
|
Mönchengladbach
Swiss fabric innovator Schoeller Textil, which celebrates its 150th anniversary this year, has taken the finishing of two-layer laminates for protective clothing and outdoor and active sportswear to a new level of production efficiency with the installation of a Monforts Eco Applicator unit.
The installation is part of an on-going programme that has seen over 25 million Swiss francs invested in new technology at the Schoeller plant over the past decade and has led to further new product developments, such as the introduction of upcycled Econyl yarns by Aquafil and the PFC-free ecorepel Bio technology, based on renewable raw materials, as new components for the company’s industry-leading membranes.
Manufacturing in Switzerland comes with environmental responsibility – the country has consistently ranked Number One worldwide in the Environmental Performance Index (EPI) and as a consequence, Schoeller has had to meet standards even higher than in surrounding European companies. Schoeller became the first textile company in the world to receive bluesign certification back in 2001. It excludes all environmentally harmful substances from the manufacturing process, sets guidelines and monitors their observance for environmentally friendly and reliable production.
Further, the company has a close cooperation with the environmental authorities in Switzerland and has also gone to great lengths to ensure no emissions or noise come from the Sevelen plant – which is in both a rural and residential area – and that it blends naturally into its immediate environment.
The advantages that can be provided by the Monforts Eco Applicator for water, energy and raw material savings were a natural fit for the company’s plant, according to the manufacturer. It has been designed to provide significant energy savings with reduced liquor application, eliminating the need for a conventional wet-on-wet padder and employing trough and roller techniques to apply just the required amount of liquid/coating to fabrics via contact with the roller.
Schoeller already operates two 2.4-metre-wide Montex stenters, the most recent being a 60-metre long, ten-chamber unit. This has a very long feed-in area, since for some laminated materials it is necessary to use two A frames for feeding in the different materials, as well as accommodating padding and laminating/coating and bonding machines.
Both stenters are connected to a heat exchange system. On the latest stenter, the waste air also goes through the heat exchanger to heat up the fresh air, providing two sources of recycled energy – both air and water. Half of the energy used for warm water at the plant is gained through heat recovery. The energy is harvested from the waste air of the steam boilers as well as the stenters, and the residual heat of the recovered steam condensation.
The Eco Applicator has been integrated at the start of the second Montex line at the Sevelen plant and its prime function is to make substrates for Schoeller’s membranes hydrophilic on their inner side and hydrophobic on the outer side in a single pass – although a further 20-25 different finishing treatments are also carried out on the line.
“It’s not possible to finish the layers individually, prior to hot melt laminating so the fabrics and membrane films are dyed separately prior to being laminated, and then finished together by the Eco Applicator before going to the stenter,” explained Michael Killisperger, Manager of Schoeller’s finishing and coating department. “The Eco Applicator is designed for minimal application, and we can measure the moisture humidity at the entrance of the unit and then after both the first and second passes through it.”
“Ideally we’re looking for 20% residual content – 10% on each side. Most of these membranes are highly elastic so high control of the fabric tension is also required to prevent the creation of stripes. This can also be controlled at various points within the unit.”
Business intelligence for the fibre, textiles and apparel industries: technologies, innovations, markets, investments, trade policy, sourcing, strategy...
Find out more