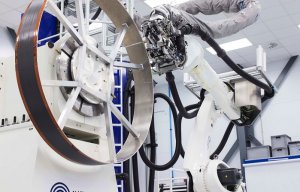
NCC’s £36.7 million iCAP is the latest boost for the UK
Opinion
The big problem with 3D printing as a potentially DIY-driven new force in manufacturing is that not much that’s being produced on an entry-level system so far looks like it’s worth owning – or even throwing away for that matter. How is it possible to get really excited about plastic toys that look like rejects from a McDonald’s Happy Meal and create yet another problem for the environment, however much fun the makers had?
10th October 2013
Adrian Wilson
|
UK
The big problem with 3D printing as a potentially DIY-driven new force in manufacturing is that not much that’s being produced on an entry-level system so far looks like it’s worth owning – or even throwing away for that matter.
How is it possible to get really excited about plastic toys that look like rejects from a McDonald’s Happy Meal and create yet another problem for the environment, however much fun the makers had?
True, bespoke designs such as the Francis Bitonti dress shown at the recent New York Fashion Week are intricately fascinating – especially since they are now said to possess true drape – but then you learn that they involved around 400 hours of printing. And they’re still virtually unwearable for any period longer than a jaunt down a catwalk.
What prompted these admittedly uncharitable thoughts was visiting the exhibition that’s been running over the past few months and ends on October 29th at the Design Museum in London: The Future is Here: A New Industrial Revolution.
On this evidence, it isn’t. Or if it is, it’s a very confused future.
There were a few carbon fibre parts, of course, a few nods to mass customisation, a Mi Adidas customisable trainer and a Puma one designed to degrade, as well as a robotic nesting and cutting system for wooden children’s toys based on what’s been used in industry for decades.
But where were the real stories to accompany this exhibition and where was the ‘Wow!’ factor?
There was not much to illustrate why the latest planes are increasingly being made from carbon fibre composites, for example, as opposed to steel. Or why BMW has so far invested €600 million and created 1,500 new jobs in the conviction that it can achieve the same mass transformation for cars.
Series production of the BMW i3 – the world’s first purpose-designed electric vehicle – began just last month and this is the first time that carbon fabric composites have been used in automotive volume production.
If called upon, I’m pretty certain the corporation would have been keen to contribute something spectacular to get its message across to the UK’s general public.
Stratasys, as the most high-profile manufacturer of 3D printing technology would surely have been another key resource.
Only this week, at the annual board meeting of the National Association of Manufacturers (NAM) in Washington, its CEO David Reis was calling for increased collaboration between industry, government and academia.
“Additive manufacturing or 3D printing can fundamentally change many aspects of the manufacturing process,” he said. “It brings new agility and efficiency and can help manufacturers keep production at home. It is imperative, however, that technology providers, manufacturers, universities and government work together to help fulfil the promise of this impressive and impactful technology.
“Many talk about additive manufacturing as a ‘disruptive’ technology, but these are the same production materials that many engineers and manufacturers are already used to working with,” added vice-president of global marketing Jon Cobb. “In our view, additive manufacturing will not replace many of the traditional manufacturing processes, but rather complement how a good portion of manufacturers are already delivering products to market in a more efficient and customized way.”
According to Lux Research, 3D printed parts will be an $8.4 billion global market in 2025 led by the automotive, medical and aerospace industries. Stratasys believes that greater awareness of the capabilities of 3D printers, advancements in materials and increasing affordability will play a significant role in driving this growth.
There was little sense of this vast potential at The Future is Here: A New Industrial Revolution, which seems like a missed opportunity. Overall, the impression was that it was curated solely by design enthusiasts with extremely limited input from the manufacturing world.
Business intelligence for the fibre, textiles and apparel industries: technologies, innovations, markets, investments, trade policy, sourcing, strategy...
Find out more