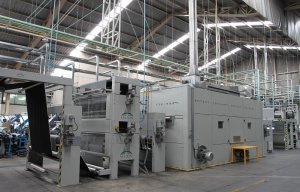
Continuous developments for denim
Exploiting multifunctional spray coating and thermo-stretch and skew technologies for more efficient production.
14th May 2025
Innovation in Textiles
|
Amsterdam
Monforts denim customers were very much to the forefront at the latest Kingpins Amsterdam exhibition held from April 16-17 at the city’s Sugar Factory.
It’s no accident, for example, that the advanced denims which have dominated the show’s Most Sustainable Product (MSP) displays over the past four years are from mills employing resource-efficient Monforts technologies including Montex stenters, Monfortex Shrinking ranges, Eco Line denim finishing systems and Thermex dyeing ranges.
“Monforts Montex stenters are the industry standard in denim finishing and many of the over 900 Monforts Thermex dyeing systems operational in the main textile producing countries are also devoted to this sector,” says Monforts head of denim Hans Wroblowski. “New performance and lifestyle denims are achieving success on the market by exploiting multifunctional spray coating and thermo-stretch and skew technologies on our ranges for more efficient production and significant increases in energy savings.”
While the Kingpins MSP is not a competition, these fabrics are singled out both for their thoughtful and eco-conscious construction and ease of converting into fully-fashioned denim jeans.
Eight of the ten fabrics in the 2025 MSP showcase were manufactured by the Monforts companies Arvind (India), Diamond Corduroy (Pakistan), Isko (Turkey), Naveena Denim (NDL), Orta (Turkey), Saitex (Vietnam), Soorty (Pakistan) and Textil Santanderina (Spain).
Stretch Yourself
Seven of the world’s most progressive denim mills – all of them Monforts customers – also provided the advanced denim fabrics for a design exploration project by 30 fashion students at the House of Denim Foundation’s Jean School in Amsterdam – the first and only denim educational institution in the world – in cooperation with The Lycra Company.
This project resulted in the ‘Stretch Yourself’ exhibition at Kingpins 2025, with fabrics supplied by Turkish companies Bossa, Calik and Orta, Naveena and Soorty from Pakistan, DNM Denim in Egypt and China’s Advance Denim.
“What excited me about this project was that we started with an educational segment on sustainability and innovation involving all the mills and kept it open for the students to design whatever they felt like,” said Mariette Hoitink, co-founder of the House of Denim. “The mills provided the students with super special fabrics and the students worked day and night to come up with the final results and took a totally unexpected take on stretch denim.”
Cellulosics
Cotton remains king in denim production, but Lenzing’s Tencel and Ecovero cellulosic fibres are increasingly finding favour in denims for providing soft hand feel fabrics.
In Amsterdam, Lenzing Hong Kong showcased its Application Innovation Collection 25 developed with mill partners including a variety of sustainable new styles from Monforts customers including Advance Denim, Naveena, Soorty, TCE Jeans (Vietnam) and US Denim Mills (Pakistan).
“Our team continues to communicate with the industry – from supply chain partners to brands and designers – to exchange marketing information and participate in trend developments,” said Dennis Hui, business development manager at Lenzing Hong Kong. “This latest collection is based on meeting demand from global brands with a variety of outfits with different wash effects.”
Sensitive fibres
Monforts Eco Line range concepts for denim enable the processing of high-quality and reproducible fabrics which are stretched and skewed far more gently than with conventional range combinations, which is advantageous in processing more sensitive fibres.
The ‘double rubber’ version of a Monforts Denim ranges comprises two compressive shrinkage units and two felt calenders in line, for super elastic and bi-elastic materials. Additionally, the combined drying, stretching and skewing functions for denim fabric are possible with the ThermoStretch unit, which can also include a Monforts EcoApplicator unit for the minimum application of necessary finishing chemicals.
Econtrol
Monforts denim customers are also reaping the benefits of the Econtrol* and Econtrol TC-A continuous process for the dyeing of woven cotton, cotton/synthetics and cellulosic like Tencel fabrics in which reactive and other dyestuffs are fixed into the fabric in a one-step dyeing and drying operation with a controlled combination of steam and air.
The entire pad-dry process takes just two-to-three minutes at a temperature of between 120-130°C and a relative humidity volume of 25-30%.
“Many of our denim customers are now using their existing Monforts technologies within integrated finishing mills to develop new in-house processes and further improve their ecological performance,” observes Hans Wroblowski. “We continue to work closely with them on a variety of interesting new projects that eventually result in many of the forward looking denim jean styles that are to be found at successive Kingpins shows around the world.”
* Econtrol is a registered trademark of DyStar.
Business intelligence for the fibre, textiles and apparel industries: technologies, innovations, markets, investments, trade policy, sourcing, strategy...
Find out more