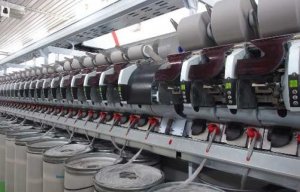
New Autocoro 9 VTC for increased profitability
Recycling Xtreme can process short mechanically recycled fibres with an extremely high raw material efficiency.
21st July 2025
Innovation in Textiles
|
Nijverdal, Netherlands
Spinning Jenny, based in Nijverdal, Netherlands, has just delivered 50,000 towels, made from yarns containing 40% content from regenerated military clothing and emblazoned with the logo of the NATO summit, to the Dutch government.
The towels were produced as gifts presented to all of the people involved in securing June’s NATO Summit in The Hague.
Dedicated to incorporating a high percentage of recycled short fibres into new fabrics, Spinning Jenny, founded in 2020, is operating a Saurer Autocoro spinning machine that has been specifically adapted for recycled fibres.
“Because we were able to build a new spinning mill like this from scratch, we could configure the processes exactly as we wanted,” says company founder Paula Gerritsen. “This gives us a competitive edge and our factory is almost fully automated. We have three production halls covering over 6,100 square metres with only four people working per shift.”
Recycling Xtreme
Developments at Spinning Jenny and other processors of recycled yarns around the world – including Giotex in Mexico, which manufactures purely 100% recycled content yarns – have contributed in turn to the development of Saurer’s latest Autocoro 11 Recycling Xtreme rotor spinning system which is capable of processing the shortest mechanically recycled fibres with an extremely high raw material efficiency.
The Autocoro 11 can accommodate up to 816 spinning positions over a length of more than 100 metres and its Synchropiecing 60 technology enables 60 piecers to start simultaneously and get up to speed in just a few minutes. New self-cleaning yarn guides, whether for pure cotton or blends with recycled fibres, significantly extend cleaning intervals and the latest machine design minimises the surface area for deposits. An integrated pneumatic cleaning system further ensures absolute cleanliness for maximum efficiency and minimum maintenance.
“We can switch it on and produce smoothly and that’s what counts for us,” says Burhan Kaplan of Biska Tekstil, which is now operating 18 long Autocoro 11 machines. “We need a quick overview and the LEDs on each machine give us exactly that – an immediate performance picture, without unnecessary travel. This gives us full production reliability and allows us to deploy our staff more efficiently.“
Cost savings
Increasing the use of recycled cotton fibres – which, for example, are on average 19% cheaper than conventional raw cotton in India – is also a promising way to save costs.
Although conventional raw cotton can be processed with up to 30% higher productivity compared to recycled fibres, this is often not enough to compensate for the high raw material costs. Recycled fibres offer a more economical solution but require precise adjustments to the spinning machine. By fine-tuning the yarn twist, speed of the opening rollers and rotor size, it is still possible to achieve a yarn quality that almost matches that of raw cotton. The Autocoro 11’s wide range of adjustment options open new ways for spinning mills to achieve greater profitability and flexibility in yarn production.
In addition, the Autocoro 11 Recycling Xtreme edition offers more options for processing mechanically recycled fibres, which are extremely short and generate a lot of dust and fly. Recycling Xtreme features a new cleaning system for the rX yarn guides and dirt-repellent surfaces for the opening rollers. The fibre beard supports of the SE 21 spin box can also be easily adapted for very short fibres.
The patented new rotor cleaning technology on the Doffing Cleaning Unit (DCU) keeps the rotor groove clean and an extraction system inside the machine removes waste even more efficiently. With an innovative three-chamber system, the waste can be collected and easily fed back into the spinning process. The Synchropiecing 60 technology increases the Autocoro 11’s piecing capacity by 65%, allowing it to maintain high efficiency even with the high breakage rates that typically occur when using recycled fibres.
Energy savings
Energy is the second largest cost factor in automatic rotor spinning mills and the Autocoro 11 minimises electricity costs by up to 10% compared to the previous generation, immediately increasing profitability for mills.
Compared to older rotor spinning machines, the savings can be up to 48%. Yarns spun on the Autocoro 11 also have the lowest energy consumption of all spinning processes.
Saurer has fundamentally redesigned the suction system and air logistics of the Autocoro 11. With modified ducts and a significant increase in capacity, the new supply ensures resistance to pressure fluctuations, supported by modern air filter systems and a revised electronic control system.
Equipped with powerful yet energy-saving drives and innovative electronic components such as optimised power supply units, the Autocoro 11 makes a decisive contribution to a positive energy balance. Even with moderate energy prices of €0.10 per kWh and relatively short machines with 480 spinning positions, spinning mills can achieve considerable cost savings in the six-figure range year after year, for each individual machine.
“We are really excited about the Autocoro 11, with savings of up to 30% in energy costs compared to our semi-automatic machines and an impressive 10% compared to previous Autocoro models,” says Fahri Polat, owner of a second Turkish company Polat İplik Tekstil, which is also employing Autocoro 11 machines. “This shows how progress is redefining our efficiency.”
Business intelligence for the fibre, textiles and apparel industries: technologies, innovations, markets, investments, trade policy, sourcing, strategy...
Find out more