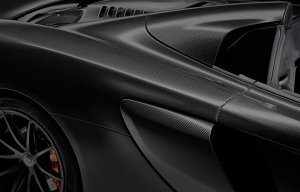
Scaling-up carbon fibres to move the needle for automotive
Key topics covered at GO Carbon Fibre Online 2021 (27–28 April) were the impact of COVID-19 on the carbon fibre industry, opportunities for growth and barriers to adoption.
10th May 2021
Innovation in Textiles
|
Online
James Bakewell reports
Strong, stiff and light in weight, carbon fibre-reinforced plastics (CFRPs) have – over the last two decades or so – become increasingly attractive for the production of parts for a number of different sectors. As such, between 2009 and the end of 2019, the carbon fibre industry experienced a decade or so of uninterrupted growth, according to the Joint Managing Director of Hofheim am Taunus, Germany-based CarbConsult, Dan Pichler. He told the conference: "Until a year ago, it was all going so well. We saw demand for, and supply of, carbon fibre increasing by, on average, 11% a year. During this time, the industry more than doubled in size, from producing 40 kt of carbon fibre a year in 2010 to over 100 kt a year in 2019."
Then, towards the end of 2019 and through to early 2020, the human coronavirus (covid-19) pandemic hit. The impacts of this were severe globally and the carbon fibre industry was not exempt. Certain markets for the material were hit hard. In the commercial aviation sector in mid-to-late 2020, for instance, international air travel was less than 10% of what it would normally have been, and it is unlikely to return to pre-covid levels until at least 2024. The building of commercial aeroplanes has therefore stalled somewhat. The CFRP-intensive A350 was built at a rate of 12 per month pre-pandemic; now only five are being produced each month. Production of the 787 is down from 14 a month to six. As such, while the aerospace industry was consuming over 20 kt of carbon fibre a year in 2019, Pichler said it will consume only approximately 14 kt in 2021.
In the automotive market, Pichler said that vehicle production was also stymied by the pandemic—the manufacture of light vehicles in Europe in 2020, for instance, dropped by 20% in comparison with 2019 and by 15% in the USA. The automotive industry is already in the process of recovering, but its use of CFRP is still in its infancy – limited by the high cost of the material to, with a few notable exceptions, niche and high-performance vehicles – and today accounts for only 10% of the total market for carbon fibre.
The wind energy industry, on the other hand, was more or less unaffected by the covid-19 pandemic. Between 2015 and 2018, 50,000 MW of new capacity (around 27 000 new turbines) was installed each year. This figure rose to 60,000 in 2019 and 93 000 MW (approximately 30,000 new turbines) in 2020. Similarly, Pichler said that in 2020 it was "Christmas in July" for the sporting goods industry, as furloughed and stay-at-home workers splurged on golf clubs, boats and bicycles with which to entertain themselves during the pandemic.
Despite these positives, Pichler said that demand for carbon fibre grew by only 1% in 2020, compared with 2019, with a similar level of growth expected for 2021. Demand for carbon fibre from the aerospace industry will be down by 27% in 2020 and will be down by 14% in 2021, but will increase by 8% and 3%, respectively, from non-aerospace markets. In terms of value, however, the carbon fibre market shrunk by 6% in 2020 and will shrink by 2% in 2021.
Any improvement in this situation will depend on how global economies recover from the covid-19 pandemic, but it was clear from the conference that the carbon fibre industry has significant potential from growth over the next decade or so.
In the wind energy market, Pichler expected installed capacity to increase at a compound annual growth rate of 17% through to 2025. The average rotor diameter of wind turbines is likely to increase from around 90 m in 2015 to around 160 m in 2026 and, to compensate for their increased weight, the proportion of blades made from CFRP will increase correspondingly, from 25–30% to approximately 40%. As such, Pichler said, the amount of carbon fibre consumed by the wind-energy industry could grow from 16 kt in 2015 to more than 40 kt in 2026.
Another speaker at the conference, Product Manager for Wind Power at Kolding, Denmark-based pultrusion specialist Fiberline, Christian Vogl, was more bullish. He told delegates that his company would need 14–18 kt of carbon fibre by 2023 to satisfy the demands of its wind-energy customers and that, by 2028, demand for carbon fibre from the wind energy industry as a whole would reach somewhere between 120 and 160 kt.
There could similarly explosive growth in demand for carbon fibre from the automotive industry, too. The physical properties of CRRPs make them highly suitable for the manufacture of battery housings for electric vehicles, but it is perhaps in the production of lightweight high-pressure vessels for the storage of hydrogen in fuel-cell vehicles where they will truly find their niche. Indeed, the Managing Director of Vaxjo, Sweden-based Connectra Global, Andrew Mayfield, told delegates that, even if the ambitious targets for the introduction of fuel-cell vehicles announced by governments around the world are not met, somewhere between 30 and 58 kt of carbon fibre will be needed for the manufacture of high-pressure vessels.
To exploit these opportunities, however, the carbon fibre industry will have to solve a number of key problems. The first is cost; carbon fibre is currently prohibitively expensive for many applications. Second, the environmental impact of manufacturing carbon fibre is significant—a potential deterrent for many potential customers. Finally, more production capacity will be needed. Given that a 1.5-kt-a-year carbon fibre line can cost around €50 million, and take two years, to get up-and-running, how many manufacturers will be willing to take the risk in the current economic climate?
The first two problems could be solved – at least in part – through the use of alternative precursors. Typically, carbon fibre is produced from polyacrylonitrile (PAN), the price of which is tied to that of oil, which has been both high and unstable in recent years. A Senior Lecturer at the University of Limerick in the Republic of Ireland, Maurice Collins, told the conference that lignin – a waste product from the paper and pulp industry – could be a viable alternative.
Working as part of the European Union (EU)-funded LIBRE project, Collins and his colleagues have developed scalable, economical and more environmentally friendly techniques for the spinning, stabilising and carbonisation of lignin/bioploymer precursor fibres. These techniques yield carbon fibres that are 50% cheaper than conventional carbon fibres and – crucially – demonstrate equivalent mechanical properties (a tensile strength of 2 GP and a Young’s modulus of 200 GPa). Carbon dioxide emissions associated with the production of these fibres are 66% lower than those generated through conventional production techniques, and lignin is cheap and abundant—Collins has already identified biorefineries that “have more lignin than they know what to do with.”
The final problem might only by solved by new, disruptive entrants to the market. The conference heard from Tim McCarthy, the Commercial Officer of LeMond Carbon Inc—a company established in Oak Ridge, Tennessee, USA, to produce low-cost carbon fibre for high-volume markets. LeMond is in the process of commercialising a number of processes for the cheap and efficient production of carbon fibre, including an oxidisation technique developed at Deakin University in Geelong, Victoria, Australia that – it claims – requires 75% less energy, and also reduces the amount of process equipment by 75%, compared with conventional techniques. These factors, it adds, will help to make the production of low-cost carbon fibre scalable at a velocity that can keep up with the market demand.
Like many sectors, the carbon fibre industry has experienced some dark times through the covid-19 pandemic. Its future, however, looks bright.
Business intelligence for the fibre, textiles and apparel industries: technologies, innovations, markets, investments, trade policy, sourcing, strategy...
Find out more