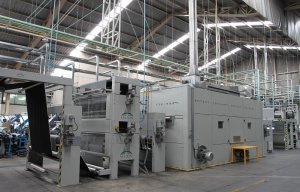
Continuous developments for denim
A significant number of Monforts denim manufacturing customers will be heading over to the UK next month.
16th November 2018
Innovation in Textiles
|
Mönchengladbach
A significant number of Monforts denim manufacturing customers will be heading over to the UK next month, when Denim Première Vision is held in London for the very first time. The event takes place from 5-6 December, at the historic Old Truman Brewery on Brick Lane, in London’s completely regenerated and thriving East End.
The Première Vision team is looking to create a similar atmosphere to that achieved in Paris in November 2017, when the Denim Pop Up Street was held each evening after the Denim PV show in the Paris Marais neighbourhood. This drew sizeable crowds to the boutiques of atelier brands and artists, along with workshops, galleries, shopping and bars.
Among exhibitors at the December 2018 London edition of Denim Première Vision will be major players from India and Pakistan – the two countries which have come to dominate the global market for denim fabric and denim jeans production over the past ten years. Spearheading a lead in sustainable denim production are companies such as Pakistan’s Soorty and India’s Arvind – both of whom have recently installed Monforts Eco Applicators at their denim manufacturing mills.
As an alternative to conventional padding, especially for wet-in-wet solutions, the Monforts Eco Applicator can significantly reduce the thermal energy required for drying prior to the stretching and skewing of the denim fabric, according to the manufacturer.
Soorty is a major producer of denim fabric and jeans, now employing some 22,000 people across its operations, which are largely based in Karachi, Pakistan. It has recently established a new, award-winning garment making-up department and office in Bangladesh, as well as a design studio in Amsterdam. Among its prestigious clients are C&A, Calvin Klein, Dorothy Perkins, Esprit, H&M, Lee, Mango, Tommy Hilfiger, Tom Tailor and Zara. The company installed an Eco Applicator two years ago, as part of the opening of a second denim manufacturing plant in Karachi, which increased the company’s finished woven denim capacity to some 5.5 million metres a month.
The Eco-Applicator immediately slashed the company’s denim finishing costs, as verified by an in-depth sustainable production study carried out with the Swiss-based chemicals giant Archroma, says the company. “Sustainable denim is our passion and we are investing more and more in order to achieve our objectives,” explained the company’s Senior Marketing and Product Development Manager Mansoor Bilal.
Monforts is now going a stage further in addressing resource efficiency by combining the Eco Applicator with its ThermoStretch unit in the latest Eco Line concept. The Monforts ThermoStretch unit carries out the skewing (weft straightening), stretching and drying in a continuous process.
“The Eco Line system reduces energy requirements and losses, increases thermal transfer and keeps the drying energy on the textile material longer,” said Monforts Area Sales Director and Head of Product Management for Denim, Hans Wroblowski. “As a result, significant energy savings are being achieved.” Arvind has recently installed India’s first integrated Monforts Eco Line which can handle fabric widths of 1.8 metres and operate at high speeds of up to 80 m/min. It is operating alongside four Montex foam finishing stenters, which are also able to handle this same width of material.
The Eco Line system is designed to reduce energy losses and energy use, increase thermal transfer and keep the drying energy on the textile material longer, so that it can be used very efficiently. As a result, energy savings of up to 50% can be achieved. Exhaust air energy can also be reduced to a minimum, which has a positive effect on the emission load into the atmosphere. Arvind’s current annual denim capacity is now 110 million metres and some key initiatives have been specifically aimed at reducing the use of energy, water and chemicals.
Monforts meanwhile plans to introduce further innovations for denim during 2019.
Business intelligence for the fibre, textiles and apparel industries: technologies, innovations, markets, investments, trade policy, sourcing, strategy...
Find out more