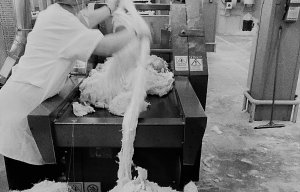
Säntis expands trademarks for RCO100
Annabelle Hutter, Creative Director, Säntis Textiles.
1st February 2022
Innovation in Textiles
|
Singapore
Säntis Textiles is a Swiss, family-owned textile company based in Singapore, with offices in the UK, USA, Indonesia, Thailand, Turkey, China, Egypt and Pakistan. Since 2016, the company has been developing 100% recycled cotton yarns from cotton waste based on a process called RCO100. In 2021, through its ongoing partnership with fashion brands such as Tommy Hilfiger, Calvin Klein Jeans and Lacoste, the company recycled a record-breaking 100,000 tons of pre-and-post-consumer cotton waste.
IIT: What is involved in the RCO100 process?
AH: It’s the first of it’s kind, and we use pre-consumer industrial waste and post-consumer cotton garment waste to produce 100% recycled OE cotton yarns up to Ne20 and ring compact yarns up to Ne30. Our RCO100 technology allows for a process which is all mechanical, with no chemistry, chemicals or regenerative fibres involved.
IIT: Where is the RCO100 cotton produced?
Our main RCO100 supply chain is in Turkey with our partner Kipas. We use mainly local pre-consumer industrial waste. Post-consumer we can import from the EU countries.
IIT: What certifications does it have?
AH: All of our RCO100 yarns and fabrics are GRS (Global Recycling Standard) certified and come with the respective transfer certificates. This applies to the supply chains as well. We also have Oeko Tex and ISO certifications.
IIT: How do you trace its progress through the supply chain and guarantee authenticity?
AH: Since the conception of RCO100 in 2016, traceability was an aspect which we were very invested in. We control the material sourcing process by using only GRS certified material suppliers and add our own audits. In addition, we work with the company Fibretrace which provides us with tracer technology to make our products unique in respect of traceability and block chain technology for the customer to trace back the RCO100 product through the whole supply chain. We are also working to collaborate with brands and their end consumers through interfaces that showcase the entire supply chain.
IIT: You are gradually introducing more post-consumer waste into products. What are the main hurdles and limitations to this at present, and how could they be overcome?
AH: Post consumer material is always a challenge because we only have limited knowledge about the original raw material and we do not know how many times the garments have been washed. Contamination is another issue. So we have to separate carefully and then blend accurately, using our extensive know-how and data base to achieve the best possible ratios and yarn results. By now we have six years of experience and big factor of RCO100 is of course our own developed and designed recycling system with a very gentle mechanical opening process, avoiding fibre damage as much as possible.
IIT: What are the chief advantages of being a Swiss-run company headquartered in Singapore?
AH: Mainly it is the connection between the European main markets and the textile centres in Asia. Singapore is like Switzerland! It is super efficient and a developed economy. To link the two bases we are able to speed up technologies and services for our customers and supply partners. Our Swiss DNA also keeps us grounded and in touch with nature – it’s an element we grew up with as a family and has translated into our work and products, especially now with RCO100.
IIT: Could you say a little about the formation of the company and its intentions – the where and why?
AH: Hailing from Switzerland and a family background of textile and engineering, my father Stefan has 30 years of experience in the textile industry. With a focus in Asia, he worked at Rieter and also as global sales director for Hualon Corporation. In 2005 he built up Säntis Textiles into a leading textiles company, initially for technical and home furnishing fabrics with locations in China, Vietnam, Indonesia, Pakistan, Turkey and additional sales offices in the UK, Germany and USA. His foray into sustainable and specifically recycled textiles came from a passion to find environmentally conscious solutions for both technical and garment fabrics. He started by developing recycling PET bottles for home furnishing solutions which eventually became commercially viable. Then in 2016 he went on to develop the technology for RCO100, which is still the only 100% mechanically recycled cotton fully commercialised on the market today. Säntis Textiles currently ships approximately eight million square metres of technical, home and RCO100 fabrics per month to the main markets – Turkey, Europe and USA. There is also interesting growth in the Asian market where quality approved fabrics are also become a big segment.
At heart, Säntis Textiles is still very much a family company. Following in the footsteps of my father, I have been leading RCO100 projects since 2020, liaising with brands and developing creative tailor-made solutions for brands to forge ahead with their recycling initiatives. Most recently, these projects have focused more on incorporating closed loop systems.
The core values of the company from the beginning were to provide a more holistic, personable connection between client and the product which results in higher quality and greater sustainability – an element which the textiles industry values now more than ever.
IIT: How many employees does the company have today?
AH: In all mentioned locations Säntis Textiles relies on a team of approx. 120 employees with approx. 90 engaged in quality control at the various production sites. At every stage Säntis Textiles provides its own quality control to assure top quality is shipped to its customers.
Business intelligence for the fibre, textiles and apparel industries: technologies, innovations, markets, investments, trade policy, sourcing, strategy...
Find out more