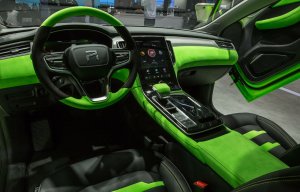
Alcantara shines at Auto Shanghai 2021
Immersive seats covered with a velvet made from 100% recycled polyester extend to the floor.
3rd July 2023
Innovation in Textiles
|
Eden Prairie, MN, USA
Advanced materials produced using Stratasys J850 TechStyle 3D printers feature in the interior of the new Peugeot Inception concept electric vehicle – achieving a level of resolution that would not have been possible with traditional embellishment methods.
The Inceprion has a minimalistic cockpit devised by design director Matthias Hossann to support the car’s aim of reinventing the driver experience. Immersive seats covered with a velvet made from 100% recycled polyester extend to the floor and feature 3D patterns created with the Stratasys 3D printing technology.
“At Peugeot, we always like to combine function with aesthetics,” said Maud Rondot, of the Advanced Design team at Peugeot. “Our objective with the Inception’s seating area was to modernise the velvet material used and decompartmentalise the design by extending it to also serve as a visually impactful floor mat.”
Where the floor area space would typically need to be treated with a protective overlay, the Inception concept leverages direct-to-textile 3D printing to deliver a unique combination of functionality, texture and aesthetics which would not have been achievable with other technologies.
“Although we have access to relatively flat designs with current embellishment methods, it is not possible to build thickness and height,” said Rondot. “It is thanks to 3DFashion technology that we could 3D print directly onto the flexible material. Often, there is a delta between what we imagine and what we can obtain, so it was quite magical to see our idea arrive precisely as envisaged and with a remarkable quality of execution.”
The team selected a metallic shade for the velvet, which is designed to play with light before using the printer to create the semi-transparent ‘micro-architectures’.
“Instead of covering the whole stretch of material, it was really advantageous that we could leave the velvet visible,” Rondot said. “3D printing allowed us to modify and reprint the files very easily, but also important is its durability and efficiency – as a technology it doesn’t require moulds, which is revolutionary in terms of industrialisation.”
Business intelligence for the fibre, textiles and apparel industries: technologies, innovations, markets, investments, trade policy, sourcing, strategy...
Find out more