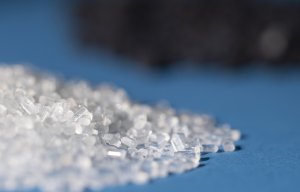
Polypropylene recycling plan for Asia
New plant is using the latest generation automation technology, to complete projects faster.
19th May 2022
Innovation in Textiles
|
Orlando, FL, USA
A purification process for recycling polypropylene (PP) waste developed by PureCycle Technologies, headquartered in Orlando, Florida, uses less energy and has lower carbon emissions than new plastic production.
These are the chief findings of the company’s first Environment, Social, and Governance (ESG) Report which has just been published and includes third party preliminary Life Cycle Assessment (LCA) data.
PureCycle’s recycled PP provides an alternative to high-cost carbon credit purchasing programmes while helping brands achieve their highest sustainability goals. The company holds a global license to commercialise the only patented, solvent-based purification recycling technology developed by Procter & Gamble for restoring waste PP into ultra-pure resin. The proprietary process removes colour, odour and other contaminants from recycled feedstock resulting in an ultra-pure PP suitable for any market.
The new report details PureCycle’s efforts to scale and optimise its recycling, harness the latest manufacturing technology systems, and leverage top tier talent to fulfil the company’s mission of transforming plastic waste into a continuously renewable resource.
Based on the design of PureCycle’s Ironton, Ohio facility, carbon emissions are expected to be 35% lower compared to new PP production and to use 79% less energy.
The plant is using the latest generation of automation technology, employing virtual reality, augmented reality and artificial intelligence to allow the company to complete projects faster, and operate with world-class performance and enhanced safety.
“As a plastic recycling technology company aiming to reduce plastic waste, partnering with leading brands to help them create sustainable consumer products and transforming the industry, it’s essential we also do our part to minimise our environmental impact and conserve resources,” said Mike Otworth, the company’s chairman and CEO. “As we continue to refine our approach, we will look for impactful, innovative ways to reduce carbon emissions and utilise less energy. This is just the beginning.”
Business intelligence for the fibre, textiles and apparel industries: technologies, innovations, markets, investments, trade policy, sourcing, strategy...
Find out more