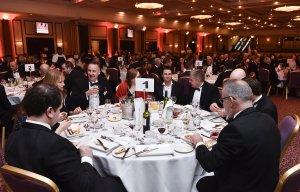
Registration open for 2017 Industry Awards Dinner
Located at the company's UK headquarters, the Innovation Centre is FORMAX's latest investment in its expanding Innovation Department.
9th September 2015
Innovation in Textiles
|
Leicester
Formax, the leading manufacturer of engineered composite reinforcements, will be highlighting the capabilities of its new Innovation Centre at the Composites Europe 2015 exhibition that takes place in Stuttgart from 22-24 September.
This facility strengthens the company's commitment to developing optimised multiaxial fabrics for the automotive, aerospace, marine, sports and industrial markets, and will also enable it to pursue new business opportunities in automated composites manufacture and non-polymer applications.
"The Innovation Centre will enable us to continue to support and grow our core business of composite reinforcements, and also allows us to expand beyond multiaxials," explained Oliver Wessely, Formax's Managing Director. "We see huge opportunities to exploit our technical textiles expertise in the area of preform manufacture and in numerous applications outside of the polymer composites industry.
The Polymer Composites Division will continue to lead Formax's market leading research into optimising multiaxial reinforcements for technically challenging applications. Areas of expertise include testing and characterisation of fabric architecture, developing new products based on novel fabric architecture, and recycling.
The group also provides process simulation support in answer to a growing need of customers. Recent additions to the Innovation Centre include a modified picture frame fixture and fabric bend testing equipment to aid in the study of fabric drape, and a fabric permeability test rig which can provide estimates of permeabilities at a given volume fraction for use in predicting resin fill time and dry spots.
The new Automation Division's activities include fibre pre-processing (including tow spreading), fibre placement for automated net shape 2D preform manufacture, and automated 3D preform manufacture. Equipment includes a carbon fibre testing cell for use in characterisation of tow width, spreadability, filament orientation and filament breakage, and a robot for preforming studies. A fabric ply cutting and kitting service is also available.
The group is currently collaborating with a major automotive OEM, the Manufacturing Technology Centre Ltd in Coventry, the University of Sheffield, and the University of Nottingham, in the ALPA (Affordable Lightweighting through Pre-form Automation) project.
With more than £2 million of funding from Innovate UK, this two-year programme is aiming to develop technologies to significantly reduce the cost of using composites in vehicle structures, with a focus on reduced material wastage and automated preform manufacture for resin transfer moulded composite components.
The Ceramic Composites Division will pursue non-polymer applications for Formax's technical textiles. Current projects include the combination of novel, low cost ceramics with recycled short carbon fibres for use in high performance, low cost friction applications, and the carbon fibre reinforcement of concrete, bitumen and gypsum for civil engineering use. The Division is led by ceramics expert Dr Arthur Swarbrick, who recently joined Formax from the University of Loughborough.
Business intelligence for the fibre, textiles and apparel industries: technologies, innovations, markets, investments, trade policy, sourcing, strategy...
Find out more