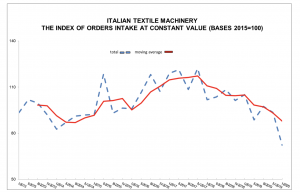
Decline in orders for Italian textile machinery in Q1
GKD will be presenting a comprehensive range of mesh and spiral fabric belts for forming, drying, and bonding of nonwovens
5th February 2020
Innovation in Textiles
|
Düren
© Gebr. Kufferath AG (GKD).
Technical weaving operation GKD – Gebr. Kufferath AG (GKD) will once again be showcasing its integrative consulting and engineering expertise for the nonwovens industry at INDEX in Geneva, the world's largest nonwovens exhibition. In keeping with the corporate vision of only creating products and solutions that make the world healthier, safer, and cleaner, GKD will be presenting a comprehensive range of mesh and spiral fabric belts for forming, drying, and bonding of nonwovens.
The company's presence at the exhibition will focus on two pioneering developments: Conducto 7690 with metallic multifilaments, and glass hybrid fabric belts with anti-stick coating. The exhibition appearance will be rounded off with tailor-made metal fabric filter media, which have been proven to set new standards in the central filters, spinning beams, and blower screens used for polymer filtration. The GKD experts, boasting many years of experience, will be on hand at the INDEX event for more detailed discussions on all topics.
“Achieving maximum process reliability and system availability is crucial in securing production efficiency and the success of products in the nonwovens industry. Conveyor and process belts from GKD perform a key task here thanks to their system-specific and product-specific mesh design and the materials used in their construction,” GKD explains.
Spunlaid nonwoven forming: metallic dissipation for hygiene products
“With Conducto 7690, a fabric design comprising polyester monofilaments and metallic multifilaments, GKD has succeeded in preparing electrostatic dissipative metal in such a way that it can also be used for sophisticated medical and hygiene products without any risks,” the company says. “This latest addition to the Conducto range facilitates between one and ten times greater dissipation of electrostatic charges than conventional belts. The metal fibres that are woven into the back of the belt do not come into contact with the product.”
“The flexible yarn produced from stainless steel fibres does not suffer from corrosion or bending fatigue and is also rugged. At the same time, it optimizes dissipation of electrostatic charges with unprecedented efficiency. The new fabric design combines these properties with the familiar benefits of all Conducto forming belts: excellent traction, homogeneous web formation, optimum nonwoven removal, and easy cleaning.”
Web bonding and drying: years of service without any material adhesion
The glass hybrid fabric belts with anti-stick coating from GKD have a proven track record of significantly increasing process efficiency, the company says. “Used as upper and lower belts in real-world applications over multiple years, they have far surpassed the high expectations in terms of process performance and product quality in exacting thermal bonding processes with highly adhesive products. The single-ply fabric design, comprising metal weft wires and fiberglass strands as the warp, makes the belts energy-efficient lightweights. A service life of multiple years minimized cleaning intervals, and high production speed underline their efficiency,” GKD adds.
“The glass hybrid fabric belts also impress with excellent transverse stability and running characteristics, even when used with large working widths and strong product shrinking forces. Their complete, high-grade PFA coating protects wires, strands, and intersections from any kind of material adhesion, even when processing highly adhesive products or using bicomponent fibres. Glass hybrid fabric belts are temperature resistant up to 250°C and do not stretch.”
Converting: field-proven and high-performance alternative
Custom spiral fabric belts, produced in-house to customer specifications, complement GKD's portfolio of tried-and-tested process belts. “These spiral fabric belts often represent an attractive alternative, particularly when using very wide or high-speed systems for production of hygiene products. Featuring high air permeability and excellent dimensional stability, they once again serve to underline GKD's integrative process and conveyor belt expertise,” the company says.
Polymer filtration: long service life, precise filtration
Multi-layer metal fabric screens, designed and produced by GKD for specific processes, ensure a long service life of the screen changers in central filters. The filter discs or cartridges, produced from up to six layers of optimized Dutch weave, are said to impress due to their high dirt holding capacity, fine filtration rates, and low clogging tendency. “In the spinning beam, media designed for specific applications optimize filtration of the fusion flow in long filters or long screens, while also extending the service life of the spinnerets. Blower screens produced from honeycomb supporting plates, employing specially pre-treated fabric designs on both sides, guarantee an even fibre flow thanks to a homogenized stream,” GKD concludes.
Business intelligence for the fibre, textiles and apparel industries: technologies, innovations, markets, investments, trade policy, sourcing, strategy...
Find out more