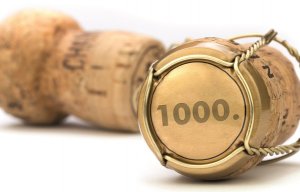
eurolaser installs 1000th large format cutting system
The company is one of the pioneering suppliers for the automotive supply industry – for all non-stop producing 2D applications in the non-metal sector.
27th July 2018
Innovation in Textiles
|
Lüneburg
Lüneburg-based company eurolaser, an ISO 9001 certified premium supplier of modular CO2 laser systems of up to 3.20 meters in width and length, will be exhibiting at the International Suppliers Fair (IZB) in Wolfsburg, Germany, in October.
The company is one of the pioneering suppliers for the automotive supply industry – for all non-stop producing two-dimensional applications in the non-metal sector.
“Conventional mechanical methods, such as blade- or die-cutting, are extremely time-consuming, complex, dust-intensive and costly. Tools wear faster and must be replaced. The cut edges often fringe and must be reworked in further steps. In addition, the contour of cutting dies cannot be changed flexibly,” the manufacturer explains.
“In contrast, contactless laser cutting is incomparably flexible, clean, fast and cost-efficient. It also allows distortion-free cutting and highest precision. Regardless of the fabric structure, processing can be carried out in all directions. Low dust generation during cutting reduces the amount of cleaning required significantly.”
“The thermal laser-processing of technical synthetic textiles melts the cut edges. As the edges do not fringe when cut, they can be processed further right away. There is no tool wear and the cut quality is consistently high.”
The eurolaser table concepts are individually configured and suitable for integration into industrial workflows 4.0. Depending on the processing material, laser sources of 60 to 600 watts are used. In addition to textile and plastics processing, eurolaser systems are also said to offer a variety of interior and exterior applications in vehicle construction in a 24/7 operating mode.
In all eurolaser systems, suitable table solutions without fixation systems are designed to ensure the optimum position of the source materials fed. In order to ensure fully automatic laser cutting directly from the roll, a conveyor belt system and a winding unit for processed textiles was developed. A dedicated nesting software by eurolaser provides for automated waste minimisation in advance.
The parallel extension of the CO2 laser systems with additional tool options enables the additional use of labelling, ink-printing and ink markers to apply information the intermediate products for downstream processes, the company adds.
Business intelligence for the fibre, textiles and apparel industries: technologies, innovations, markets, investments, trade policy, sourcing, strategy...
Find out more