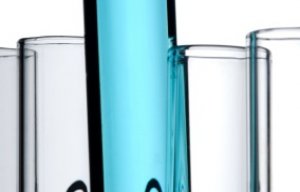
New nonwoven fibre for improved fluid management
NatureWorks announced today at the 2009 International Nonwovens Technical Conference (INTC) being held in Denver that two grades of its low-carbon footprint Ingeo bio resin are now commercially available for the production of meltblown nonwovens, fabrics widely used in such products as wipes and filters. “As interest grows in polymers made from renewable resources, equipment manufacturers, process developers, and researchers have been exploring solution
21st September 2009
Innovation in Textiles
|
Minnetonka, MN
NatureWorks announced today at the 2009 International Nonwovens Technical Conference (INTC) being held in Denver that two grades of its low-carbon footprint Ingeo bio resin are now commercially available for the production of meltblown nonwovens, fabrics widely used in such products as wipes and filters.
“As interest grows in polymers made from renewable resources, equipment manufacturers, process developers, and researchers have been exploring solutions that offer meltblown nonwoven fabrics that both perform well and achieve a lower carbon footprint than the existing petroleum-based incumbents,” said Robert Green, Director of Fibers and Nonwovens at NatureWorks.
Green was referring to meltblown fibre equipment manufacturer Biax-FiberFilm, which earlier this year conducted meltblown tests of Ingeo, made from plant sugars, not oil. Researchers at the University of Tennessee Nonwovens Research Lab (UTNRL) also evaluated Ingeo for its suitability for meltblown fabric substrates using conventional meltblowing equipment.
“Our development of an Ingeo meltblown substrate significantly broadens the variety of applications in which this material can be used,” said Doug Brown, president, Biax-FiberFilm. “An Ingeo meltblown nonwoven offers an estimated 30 to 50 percent cost savings over conventional fibre-based nonwoven roll goods and a significant advantage in price stability compared to petroleum-based products.” Brown also noted that mixing the Ingeo meltblown fibre with wood pulp or viscose greatly enhanced the material’s absorption, making it suitable for a broad range of performance wipes products.
In its development work, Biax-FiberFilm, demonstrated excellent performance of two Ingeo grades in their meltblown process. Ingeo 6252D and 6201D each provided broad processing windows and quality fabrics that meet requirements for a range of applications. The high pressure die design unique to Biax FiberFilm meltblown lines allow processing of higher viscosity grades of Ingeo, such as 6201D, offering even higher fabric strength than seen on conventional meltblowing equipment.
These recent advances provide the nonwoven market with a full range of Ingeo fabrics that can now be produced with all major fabric forming technologies from spunmelt to conventional carded nonwovens, offering the ability to meet consumers’ convenience needs with an annually renewable low environmental impact material. The attached graphic shows the significant environmental advantage Ingeo offers over conventional petroleum based products.
NatureWorks and Biax FiberFilm will present the results of this work in separate sessions at the INTC. Also at the conference, Fiber Innovation Technologies will present a paper on thermal bonding with Ingeo, and the University of Tennessee as well as Oklahoma University will review research into Ingeo mulch fabrics and fibre production.
Business intelligence for the fibre, textiles and apparel industries: technologies, innovations, markets, investments, trade policy, sourcing, strategy...
Find out more