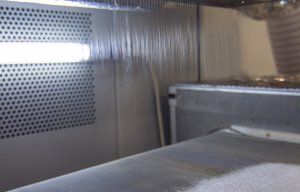
Meltspinning system upgrade for NIRI
As companies replace single-use plastic, bio-based binder applications can help bridge any performance gaps.
28th October 2022
Innovation in Textiles
|
Leeds, United Kingdom
With complete pilot-scale prototyping facilities already helping customers across multiple sectors to develop novel products and enhance and improve existing lines, NIRI – Nonwovens Innovation – is continuing its investment strategy with major new upgrades to its spray bonding capabilities.
Bespoke-engineered for the needs of the clients of Leeds, UK-based NIRI, the new equipment is specifically designed for the application of binders to both high and low loft fabrics and features a dedicated spraying rig for pilot-scale binder applications and continuous binder application.
With 87% of Europeans worried about the environmental impact of plastic and 74% about the impact on their health, the EU’s Single Use Plastic Directive (SUPD) continues to have a significant impact on nonwovens, particularly in sectors such as wipes, sanitary and feminine hygiene products, general medical supplies and devices, packaging and the food and beverage industry.
As companies replace single-use plastic products with plastic-free versions, bio-based binder application can help bridge any performance gaps. This technique can reduce linting and lead to better quality products, with improved softness and comfort, greater structural integrity and processability, improved aesthetic appearance and better surface functionality. Products developed using bio-based binder technology can be completely biodegradable and, potentially, 100% compostable.
Regulatory demands
While the environmental and sustainability benefits are clear, helping companies comply with current and future regulatory demands, the technology can also offer enhanced performance and possible cost reductions on a commercial level.
NIRI’s facilities are designed so that the pilot scale application of binder by spraying allows for more controlled impregnation which produces a more uniform end sample, for better quality control and greater certainty of prototype or final product feasibility. A controlled spray rate, together with flexibility over application distance and dwell time, allows for optimisation of the impregnation/bonding process. The new equipment is designed to apply the binders through micro-dosing, using spray jet streams running over a conveyor system. A transport conveyor supports and carries a substrate or medium while the micro-dosing unit comprising up to three flat spray nozzles sits above it. A suction slot, in-line with the spray nozzles, runs under the conveyor. Samples are belt-fed through the spraying rig where the spray applicators with their controlled flow rates apply the binder formulation to the unbonded web. Once sprayed, the web is then fed into a through-air oven to consolidate the fabric, and additives can also be used to impart specific functional properties to the final fabric.
Compared to alternative processes such as padding, the spray bonding technique requires reduced quantities of binder and water, with lower water consumption during processing and less energy during heating and drying. Given increasing consumer demand for sustainability and the current energy crisis, these can present significant commercial and reputational advantages. As the process allows for the maintenance of all or most of the loft of the fibre matrix, the low volume density characteristics are largely retained, meaning enhanced product quality.
UK commitment
In the context of the EU Directive, the UK’s Department for Business, Energy and Industrial Strategy, together with the Department for Environment, Food and Rural Affairs, published a summary of outcomes from their joint consultation into standards for bio-based, biodegradable, and compostable plastics – demonstrating a commitment to continue investment in sustainable options to replace single use plastics since leaving the EU. Noteworthy from this consultation is the response to questions around market factors which may hinder the development or feasibility of bio-based plastics, particularly as regards scale, sustainability and cost. Here, the government stated a commitment to ensuring that new technologies can succeed in the marketplace, and to continued innovation. Further, the government response states:
“The greater use of bio-based materials could provide significant economic benefit whilst reducing our reliance on finite fossil-based resources. ”
In this context, with a compelling commercial case for sustainable products, NIRI’s upgraded spray bonding facilities are an important addition to help foster the development of innovative products. Pilot-scale equipment is ideal for cost-effective and rapid prototyping for commercially viable R&D and NIRI’s facilities are designed to be modular, focused on working with clients to develop products from concept through to prototyping and then supporting scale-up.
“Regulatory changes, together with consumer demands to address the environmental impacts of plastic pollution, are a significant factor in developments within the nonwoven sector, and for our clients’ own development strategies,” said Dr Ross Ward, chief commercial officer at NIRI. “While single use plastic is high profile as an issue to be addressed – albeit a complex one that may not be solved overnight – more durable products will undoubtedly come under increased scrutiny. We are already working with clients who are using our upgraded spray bonding facilities to develop novel products, and this can only be good for the commercial and environmentally-viable future of product development across a wide range of sectors.”
This new investment was made possible with help and funding from the PAPI Project. PAPI is part-funded by the European Regional Development Fund (ERDF) as part of the European Structural and Investment Funds Growth Programme 2014-2020. In partnership with the Northern Powerhouse, it is delivered by The University of York.
Business intelligence for the fibre, textiles and apparel industries: technologies, innovations, markets, investments, trade policy, sourcing, strategy...
Find out more