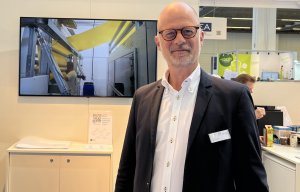
Spinnova teams up with imogo
The Dye-Max promises to slash the use of fresh water, waste water, energy and chemicals by up to 90%, compared to conventional jet dyeing systems.
2nd May 2019
Innovation in Textiles
|
Limhamn
The new imogo Dye-Max system. © imogo
Imogo, a new Swedish company formed by a team with long experience in textile processing technology, is now aiming to change the face of the textiles manufacturing industry with its new Dye-Max spray dyeing technology, to be introduced to the market at ITMA 2019 in Barcelona, next month.
While still at the prototype stage, and with a first full-scale line currently under construction and due to be demonstrated this Autumn before delivery, the Dye-Max promises to slash the use of fresh water, waste water, energy and chemicals by as much as 90%, compared to conventional jet dyeing systems, according to the manufacturer.
Its application unit consists of a closed chamber containing a series of spray cassettes with precision nozzles for accurate and consistent coverage, in combination with the patented imogo pro-speed valve that controls the volume to be applied. The chamber is equipped with an exhaust system and droplet separator to ensure that the environment around the unit is free from particles.
“The spray cassettes are a key part in the Dye-Max line,” explained Imogo’s founding partner Per Stenflo. “There is one set of spray cassettes for each of the three separate dye dispersion feed lines and they can be easily exchanged without the need for tools in less than a minute. This allows for extremely fast changeovers between different colours without the need for cleaning. And because the spray cassettes are removable, all maintenance can be performed off line. After applying the dye dispersion, the fabric is rolled onto a shaft and moved to the autoclave for deep dye fixation via heat and pressure.”
The savings in treatment water the Dye-Max achieves are due to the extremely low liquor ratio of 0.5 litres per kilo of fabric, Mr Stenflo adds. “At the same time, the low liquor ratio and the spray process require considerably less auxiliary chemistry to start with, and all of it is used in the process, which also greatly reduces the production of waste water, with only 20 litres being required for wash at changeovers. The low liquid content in the fabric meanwhile minimises the energy needed for fixation.”
The Dye-Max has a working speed of up to 50m/min with the practical speed determined by the fabric weight and application volume.
The application volumes and speeds can be pre-determined by running tests in the Mini-Max laboratory unit. “With the Mini-Max it is possible to run miniature production tests to set the precise colour recipe,” said Mr Stenflo. “This frees up valuable production time by avoiding wasteful pre-runs. The user simply sets the recipe with the Mini-Max and transfers the parameters to the Dye-Max recipe database for the system to be fully production ready.”
Imogo is partnering with fellow Swedish company ACG Kinna to build the first Dye-Max line and will be present at the ACG Kinna Automatic stand at ITMA 2019 from 23 June onwards. “We have conducted full testing of the system at the University of Borås here in Sweden and we have been more than satisfied with the quality which has been achieved,” concluded Mr Stenflo. “There can be no doubt that the textile industry will transition to more sustainable production processes and it’s not a question of if this will happen, but what will replace the current established process technologies and how quickly new solutions will be accepted.”
“There is often a hesitancy to be a pioneer in adopting and advocating new technology due to the risks involved, and government regulations and consumer pressure are still necessary to force brands and producers to adopt new technology. It is the willing pioneers, however, with whom we hope to have fruitful discussions at ITMA 2019.”
Business intelligence for the fibre, textiles and apparel industries: technologies, innovations, markets, investments, trade policy, sourcing, strategy...
Find out more