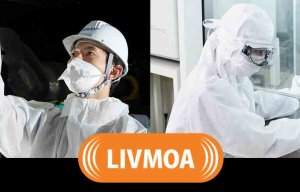
Protective clothing reduces heat stress
At present, many industries are facing huge supply chain challenges to which TenCate Protective Fabrics is not immune, says global procurement director Jelle Stratman.
23rd May 2022
Innovation in Textiles
|
The Netherlands
Since late 2021, economic activities and demand have increased dramatically. This has been due to industries and economies opening back fully post-Covid, leading to people spending more. While this is great for recovery, the surge in demand has been met by a number of imbalances popping up at the same time, leading to supply issues.
The Russia-Ukraine war had a palpable impact on global supply chains. For instance, the worldwide supply of wheat and sunflower oil have been affected because 50% of grains globally come from Russia and Ukraine, so this disruption has pushed up the prices of foodstuffs such as bread and pasta.
Within the protective clothing industry specifically, the war has led to a higher demand for aramid fibres, which are used for military applications like ballistic helmets and body armour. This higher demand has led to scarcity of supply and thus an increase in cost. This comes alongside an already tight availability of aramid polymer and fibre due to high demand in other sectors and a backlog in production output due to standstill, Covid-19 outbreaks and a lack of raw materials.
Ukraine also has an essential place in the global market of ammonia and ammonium sulphate – important building blocks in the chemical sector. With this market falling away, we see prices skyrocketing around the chemical families which are using these building blocks. Together with the gas-heavy characteristic of chemical plants, which is also trending at record-high levels, we see a perfect storm happening in the European chemical markets.
Container crisis
Furthermore, we have been faced with the container crisis in Asia, which has seen container prices increasing six-fold. Due to the differing speeds of recovery post-Covid around the world, there have not been enough containers coming back to Asia, pushing their costs up and slowing down the supply chain. New outbreaks of Covid-19 literally stopped ships entering Shanghai’s port, bringing down the reliability of on-time shipment arrival to 15%. Other regions in the world have seen decreases all the way down to 30% – placing further stress on the existing supply chains and bringing further delays to every step in the entire production process of fabrics.
The effect of this on the protective clothing industry is immense. We buy a lot from Pakistan, for instance, and where it would usually take 4-6 weeks for us to receive orders, it can now take three months and we don’t see any clear improvement in the near future, particularly with the radical measures that some countries take to battle Covid outbreaks, suddenly halting entire supply chains.
Oil, energy and chemicals
As has been well-reported, the world is currently experiencing an oil and energy crisis and the costs of these elements have skyrocketed. This has been exacerbated by the Russia-Ukraine war, which has also seen a halt on chemicals being exported from Russia. The protective clothing industry is heavily reliant on oil, energy and chemicals for its manufacturing processes, and we are unable to absorb all of the rising costs. This has a direct effect on our supply chain, as we are forced to pass along the price increases in order to stay afloat.
Also, we see that the global availability of dyes and finishing chemicals is severely impacted by several factors. The Chinese government, for example, implemented tight regulations on the dye industry during the Olympic Games in China, hindering the output of dyes and dye-acids needed for production. Furthermore, dye producers are still trying to catch up with order demand and backlog which built up during the last 18 months, after demand peaked and supply was still low due to Covid-19 and reduction of output when demand was low. Together with good demand in the automotive and paint and coatings market, we don’t see an improvement anytime soon and expect prices to remain under pressure.
Evolving approaches
With all these challenges, it’s clear that industries need to evolve their approaches in order to carry on. The challenges mentioned are global geopolitical problems that are here to stay, so industries need to carry the burden together. Within the protective clothing industry, good forecasting is critical so that we can buy materials earlier, faster and at a better price. With the uncertainty of the situation in Russia and Ukraine, being flexible is key – approving new suppliers can help avoid further supply chain issues, as well as approving new spinners around the world to work with your fibres.
Business intelligence for the fibre, textiles and apparel industries: technologies, innovations, markets, investments, trade policy, sourcing, strategy...
Find out more