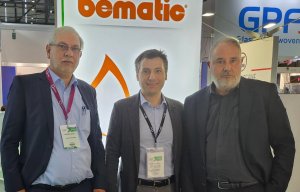
Optimising the airlaying process
Fraunhofer ITWM vs. Corona: with mathematics against the crisis
28th April 2020
Innovation in Textiles
|
Kaiserslautern
Simulations by the Fraunhofer Institute for Industrial Mathematics (ITWM) make processes in the manufacturing of nonwovens more efficient, the institute reports. “Within the anti-corona program of Fraunhofer the production of infection protection is optimized,” it states.
“Nonwovens production is currently attracting more attention than ever before from the general public, because in times of the corona pandemic, nonwovens are vital for infection protection in the medical sector and also for the protection of the entire population,” ITWM explains.
“Disposable bed linen in hospitals, surgical gowns, mouthguards, wound protection pads and compresses are some examples of nonwoven products. Especially in intensive care and geriatric care, disposable products made of nonwovens are used due to the special hygiene requirements. At the moment there are clear bottlenecks in the production of these materials. For the meltblown nonwovens class, however, it is difficult to increase production efficiency because meltblown processes are highly sensitive to process fluctuations and material impurities.”
“Although nonwovens are not all the same, the rough principle of their production is relatively similar to all industrially manufactured nonwovens: molten polymer is pressed through many fine nozzles, stretched and cooled down in an air stream and thus deposited into the typical white webs. "Meltblown" stands for the submicron fibre process whose nonwovens are responsible for the decisive filter function in face masks,” ITWM adds.
“With meltblown technology, nonwoven fabrics are produced directly from granules. A special spinning process in combination with high-speed hot air is used to produce fine- fibered nonwovens with different structures. The fibers are highly stretched by the turbulent air flow. During this process they swirl in the air, become entangled and fall more or less randomly onto a conveyor belt where they are further consolidated - a very complex process. Nonwovens manufacturers around the world are striving to massively increase their production capacities.”
Digital twin optimizes meltblown process
This is where the software of the ITWM comes into play. "Our Fiber Dynamics Simulation Tool FIDYST is used to predict the movement of the fibres, their falling and the orientation with which they are laid down on the conveyor belt. Depending on the process settings, turbulence characteristics are generated, and thus nonwoven qualities are created that differ in structure, fibre density and strength," explains Dr. Walter Arne from the Fraunhofer ITWM. He has been working at the institute for years on the simulation of various processes involving fibers and filaments.
According to ITWM the methodology is well transferable to meltblown processes. “In these processes, one of the specific features is the simulation of filament stretching in a turbulent air flow - how the stretching takes place, the dynamics of the filaments and the diameter distribution. These are all complex aspects that have to be taken into account, but also the flow field or the temperature distribution. The simulations of the scientists at the Fraunhofer ITWM then provide a qualitative and quantitative insight into the fibre formation in such meltblown processes - unique in the world in this form when it comes to simulate a turbulent spinning process (meltblown),” the institute says.
Nonwoven manufacturers benefit from simulation
“What does this mean for the industry? The production of technical textiles becomes more efficient, but the nonwovens can also be developed without having intensive productions tests in a real facility. This is because the simulations help to forecast and then optimize the processes using a digital twin. In this way, production capacities can be increased while maintaining the same product quality. Simulations save experiments, allow new insights, enable systematic parameter variations and solve up- scaling problems that can lead to misinvestments during the transition from laboratory to industrial plant.”
Making a contribution
"We want to demonstrate this in the project using a typical meltblown line as an example - for this we are in contact with partner companies," says Dr. Dietmar Hietel, head of the department Transport Processes at the Fraunhofer ITWM. "Within the framework of Fraunhofer's anti-corona program, we want to use our developed expertise and our network to contribute to overcome the crisis", reports Hietel. His department at the Fraunhofer ITWM has been pursuing research in the field of technical textiles for around 20 years. Due to its current relevance, the project not only got off to a quick start, but the implementation and results should now also be implemented quickly: The project is scheduled to run from April 15th 2020 to August 14th 2020. The kick-off meeting took place on April 17th 2020 via video conference.
“The project ‘Meltblown productive’ and the results are certainly interesting for nonwoven producers. The production of many mass products has often been outsourced to Asia in the past decades; the nonwovens manufacturers remaining in Germany and Europe tend to focus more on high-quality technical textiles. In the medium and longer term, this will also be a scientific preliminary work when production capacities in Germany and Europe are expanded by new plants. One lesson to be learned from the crisis will also be to reduce the dependence on producers in Asia, especially as a precautionary measure for crisis scenarios,” ITWM concludes.
Business intelligence for the fibre, textiles and apparel industries: technologies, innovations, markets, investments, trade policy, sourcing, strategy...
Find out more