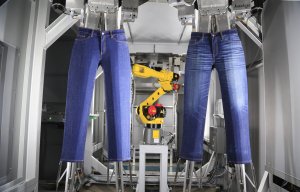
Urban Factory opens in LA
Jeanologia presented its innovative High Dynamic Range (HDR) system at last week’s Munich Fabric Start’s Bluezone.
14th September 2017
Innovation in Textiles
|
Valencia
This generation of laser has been developed to reduce laser marking times by up to 30% and increase production capacity. “The HDR starts a new era in laser production for jean finishing,” the company says. “The new hyperbolic design system, patented by Jeanologia, guarantees What you see is que you get.”
The High Dynamic Range controls the laser, increasing the dynamic contrast of tones in the images to obtain a level of depth closer to reality and thereby achieving a more natural and 3D design.
The Spanish company is an expert technology partner for top international brands in denim that want to produce in a sustainable and efficient way. Jeanologia’s solutions using the clean technologies laser, ozone and nano-bubbles aim to increase productivity, reduce time-to-market, automate processes and reduce production costs.
With the patenting of the HDR, Jeanologia says it goes a step further and re-imagines how to design in the textiles industry, enhancing the creativity, saving time and avoiding second-rate production and contributes a common language to the sector.
“Transforming the denim industry towards efficiency and sustainability is the objective that has driven Jeanologia for over 20 years. A change in the model is urgent moving the industry from being one of the most polluting, based on cheap labor towards a sustainable model,” said Carmen Silla, Marketing Manager at Jeanologia.
“Our role as a technology partner is to ensure sustainable production of jeans, which is the second most sold garment in the world after t-shirts. This way of producing must become part of the DNA of the garment and be its added-value for the consumer.”
With the process “one glass, one garment”, only one glass of water is required to complete the finishing of a denim garment. “A radical reduction in water consumption when you take into account that currently about 70 litres are needed,” the company comments.
Visitors also had the opportunity to learn about the collection Chemical Free Finishing, which is designed to eliminate the use of the harmful potassium permanganate sprayed during the finishing of jeans, thanks to the laser solution Light PP Spray; and also the Stone Flow, through which Jeanologia advances a more efficient and sustainable way of getting the stone-washed effect. By combining laser, ozone and nano-bubbles, eliminating the need for pumice stone, saving up to 70% in water usage.
Business intelligence for the fibre, textiles and apparel industries: technologies, innovations, markets, investments, trade policy, sourcing, strategy...
Find out more