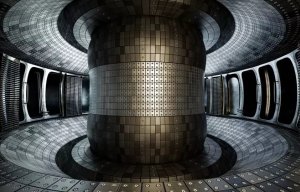
Fusion potential of silicon carbide composites
Process could be adopted by other brands to effectively tackle diaper waste in landfills.
17th November 2022
Innovation in Textiles
|
Cottsdale, AZ, USA
Dyper, based in Cottsdale, Arizona, has developed a process for turning soiled diapers into biochar, as a potentially economic and realistic solution to this major consumer waste stream.
Biochar is a carbon-rich product created through pyrolysis, which allows for waste to be transformed into a reusable commodity that can improve soil, assist in air and water purification and be used as an additive in paints and inks for improved pigmentation.
With the average infant using around 3,700 disposable diapers and more than 27 billion of them ending up in US landfills each year, diapers rank as the third leading contributor to the nation’s landfills by mass and take up to 500 years to break down, Dyper reports.
In 2023, the company will install its new Byochar reactors in select markets. When in place, they will transform something as environmentally hazardous as a used diaper into a material that can ultimately have a carbon-neutral footprint, without the use of offsets.
A leader in the premium disposable diaper category with its diapers constructed from plant-based materials and made without harmful ingredients, Dyper’s Redyper landfill avoidance programme has already diverted more than 11.5 million pounds of waste from landfills, turning used diapers and wipes into a nutrient-rich topsoil that is used in large-scale landscaping, roadside plantation and growing sod.
As Byochar technology is deployed, the process of composting in the Redyper programme will be gradually replaced.
“While there are no silver bullets to solving the plastic diaper dilemma, we feel it is our obligation to continuously look for solutions,” said Sergio Radovcic, founder and CEO of Dyper. “We’ve started with composting, fully aware of the inherent difficulties of doing it at scale. With this innovation, we will bring modular disposal technology to complement or replace composting closer to the consumer, reducing processing and transfer times. We’re excited to see our work turn waste into something more helpful.”
Biochar technology is not new, but until now has not been used to combat the disposable diaper waste problem.
Redyper currently composts diaper waste to create beneficial topsoil and Byochar will reduce the processing time from several months to minutes. In addition, an efficient Byochar reactor needs less space and electricity than a traditional composting facility and the reactors have the capacity to process two tons of diapers per day – 7,200 diapers every 10 hours, or 12 diapers a minute.
Converting Dyper diapers and wipes to biochar yields an 80% reduction in mass –100 pounds of dry diapers yields approximately 20 pounds of biochar.
In the future, Byochar may be compatible with other diaper brands, which could potentially end diaper waste altogether (4% of solid waste) but is currently not compatible with non-Dyper products. Byochar may also eventually generate carbon credits and possibly sell credits on the trading markets.
Dyper products are made without chlorine, latex, alcohol, lotions, TBT or phthalates. They’re unprinted, unscented, soft to the touch, yet extremely durable and absorbent, and made with plant-based materials such as viscose from bamboo.
They are available from select retailers including Amazon, Babylist, Grove Collaborative, Thrive Market, Whole Foods Market and Walmart.
Business intelligence for the fibre, textiles and apparel industries: technologies, innovations, markets, investments, trade policy, sourcing, strategy...
Find out more