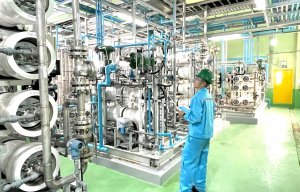
Archoma addresses wastewater issue in Thailand
The production facility specialises in polyamide 6 polymerisation and BCF yarn production.
25th February 2019
Innovation in Textiles
|
Bergamo
The new plant, which has recently undergone a test run, recovers the wastewater from the polymerisation process with a caprolactam concentration of 8-12%. Using falling film and mechanical vapour recompression technologies, the plant processes the water, so as to raise the caprolactam concentration in the output up to 80%, thus making the recovered caprolactam suitable for reuse in continuous cycle polymer production.
“This investment has taken advantage of some of the benefits provided by Industry Plan 4.0 and is part of the company production plan. The system incorporates the latest developments in technology, which allow it to reduce the quantity of heat energy used and will help us achieve the EU 2020 goals (ETS) concerning CO2 emissions,” said Nicola Agnoli, CEO of the RadiciGroup Performance Yarn Business Area.
The new plant has already proven effective in achieving a noticeable reduction in the quantity of natural gas used for steam production, as well as a generalized improvement in the quality of the output product, the company reports.
The quantity of steam needed for the lactam wastewater recovery process in the new system has fallen by about 80% (the pressure being equal) compared to the amount required for the old plant previously in operation. This reduction, in turn, has had a positive effect on RadiciFil’s overall performance: the consumption of natural gas needed for the operation of the entire production plant has dropped by about 35-40%.
Another innovative feature of the new wastewater recovery plant lies in its ability to adapt to changes in production, flexibly adjusting to the variations in the lactam wastewater input load in a range from 60% to 100%.
“The construction work for the new system was coordinated by Marco Gualteroni, engineer and site energy manager acting in the capacity of project leader,” continued Nicola Agnoli. “In all the phases of the project, the work was accomplished in collaboration with the members of the RadiciFil Technical Department and a multidisciplinary team whose members are experts in different company functions. The project also benefited from external assistance by Giovanni Algeri, an engineer who works for another Group company. Once more, teamwork proved to be the best strategy for the fulfilment of ambitious goals.”
Business intelligence for the fibre, textiles and apparel industries: technologies, innovations, markets, investments, trade policy, sourcing, strategy...
Find out more