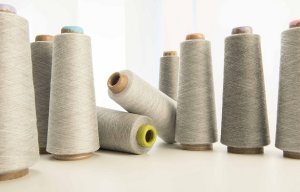
Loepfe introduces new quality control feature
The new OffColor detection for polyester yarns by Loepfe has been extensively tested in the PT. Superbtex spinning mill in Indonesia.
10th October 2018
Innovation in Textiles
|
Wetzikon
The utilisation of the new OffColor detection for polyester yarns by Loepfe has been extensively tested in the PT. Superbtex spinning mill in Indonesia. Thanks to the new OffColor detection feature of Loepfe´s YarnMaster ZENIT+, the labour-intensive and therefore expensive visual inspection of the bobbins is no longer necessary, according to the manufacturer.
The raw material for spinning synthetic fibres originates from well-controlled processes in chemical plants. This is why contamination with foreign matter occur very rarely. However, synthetic yarns like polyester can have different fibre qualities with different glossiness. Mixed-up yarns can lead to defects in the following processes along the production chain.
Today, the visual inspection of these costly errors is still very time- and labour-intensive. “We use several different polyester fibres in our spinning mill,” said Sendjaja Halim, who is responsible for the spinning mills of the PT. Superbtex Group. “Dull, Semi-Dull, Bright, and Super-Bright are the typical fibre qualities we use, and all of them have a different glossiness.” The difference can be hardly visible, when looking at the spun yarn. As an alternative to direct visual inspection of the bobbins, the inspection can be conducted under illumination with ultraviolet light. But even then, the difference is difficult to see. If the inspection is done after the winding process, and the wrong yarn is near the inner part of the cone, it is hardly visibly even under ultraviolet light.
In addition, the visual inspection can be very expensive. Mixed-up yarns can lead to defects in the following processes along the production chain, for example, during dyeing. Especially in weaving very long errors can occur, when the wrong yarn is used as warp thread. A single bobbin with the wrong yarn could lead to expensive complaints by the customer.
When spinning polyester, yarn clearers are used in most cases only to eliminate process related yarn faults, to monitor hairiness and imperfections, and to ensure the proper yarn count. Foreign matter detection is usually not necessary in polyester spinning, as the raw material originates from the chemical process.
“However, the problem of different glossiness can be solved by installing the yarn clearer YarnMaster ZENIT+ with the OffColor feature,” the company says. “The new functionality has been developed for the detection and elimination of very small colour and shade variations in mélange yarns. They can arise, when bobbins with slightly different colours are mixed up during the winding process, or the fibre blend of the differently coloured fibres change over a certain length.”
As the glossiness of the different fibre qualities used in polyester spinning and winding also vary, due to the different amounts of matting agents used in their production, Loepfe came up with the idea, to test the new feature in the PT. Superbtex spinning mill.
Extensive tests have been conducted at the largest spinning mill of the group. A Savio Eco Pulsar winding machine has been equipped with the new YarnMaster ZENIT+ including the OffColor feature. The test runs have been made with Ne40 polyester yarn of two types: super-bright and semi-dull. Various settings have been tested in order to reach the optimum performance of the OffColor detection. After triggering the set alarm limit the winding position is blocked. The winding spindle ejects the faulty bobbin once the alarm is confirmed. The operator can then remove the bobbin and the winding continue.
During the tests, wrong bobbins have been inserted on purpose. “We have been able to detect all bobbins with the wrong glossiness,” commented Sendjaja Halim.
The new OffColor detection uses the F-Sensor, which is an integral part of YarnMaster ZENIT+. In order to detect faults, the sensor illuminates the yarn from several sides. A special algorithm converts the signals resulting from reflection and transmission of the light into a luminosity difference. The reference thereby is the brightness of the yarn colour. Depending on the base-colour, the clearer adapts to the basic brightness of the yarn and is thereby able to detect colour and shade variations as well as glossiness differences.
In the event of an objectionable luminosity fault, the clearer monitors the affected fault length and cuts only once the detection stop limit is reached. By setting various parameters the user can select the optimal tolerances.
Business intelligence for the fibre, textiles and apparel industries: technologies, innovations, markets, investments, trade policy, sourcing, strategy...
Find out more