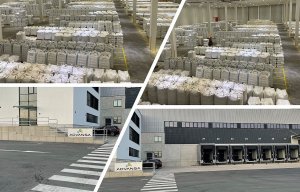
Advansa to close fibre plant in Germany
Opinion
There’s a wealth of know-how in fibres and yarns for technical textiles behind the small Dutch company Applied Polymer Innovations BV (API). Based in Emmen, it has brought together around 20 of the key specialists who have previously worked at now-vanished major European producers including Enka, Akzo Nobel, Acordis and Diolen. Today, it is largely involved in R&D and lab and pilot-scale activities.
26th February 2014
Adrian Wilson
|
UK
There’s a wealth of know-how in fibres and yarns for technical textiles behind the small Dutch company Applied Polymer Innovations BV (API).
Based in Emmen, it has brought together around 20 of the key specialists who have previously worked at now-vanished major European producers including Enka, Akzo Nobel, Acordis and Diolen. Today, it is largely involved in R&D and lab and pilot-scale activities.
Established in 2008, the company has so far focused on the development of high-end applications employing biopolymers and the niche production of mono and multifilament yarns, such as those for tyre cord.
One market, however, has come entirely out of the blue and is now taking on epic proportions for API – the sudden adoption of PLA as the polymer and monofilament of choice for 3D printing.
Speaking at the NatureWorks Innovation Takes Root conference held in Orlando, Florida, from February 17-19, the company’s Bas Krins said that API has rapidly become the largest manufacturer of PLA monofilaments for 3D printing and has been entirely sold out throughout 2013.
It has consequently employed a toll manufacturer capable of meeting demand – working around the clock – as it rushes to put in place the equipment necessary to deliver five times its currently-achievable volume this year.
The European market for PLA as a 3D printing feedstock is as yet small – an estimated 700 tons or so – but its rise has been surprisingly rapid – as much to NatureWorks as the PLA supplier as anyone else.
API produces the monofilaments for this end-use in a range of sizes and types such as flame retardant and thermochromic versions and in addition to forming the printed structures, it’s also being used in a water-soluble form as a support structure.
Over in Ireland, meanwhile, 3DOM Filament is a newly-formed company based in County Donegal, Ireland, also on a mission to supply more Ingeo filament to the 3D printing market.
“With Ingeo, 3DOM Filament will help to ensure the availability of a PLA monofilament that meets quality standards and reduces filament-related problems with 3D printing,” says NatureWorks new business chief Dan Sawyer. “While the 3Dom company is new, the team behind it has more than a decade of experience with Ingeo PLA. 3Dom is also actively involved in the research and development of Ingeo blends and additives, bringing new performance enhancements to the 3D printing community. NatureWorks is meanwhile collaborating with customer compounders and additive suppliers, and we intend to develop further strategic relationships around the world to support the growing global 3D printing market.”
The higher the quality of the printer monofilament in terms of roundness, diameter and consistency, the better the results of the 3D printing experience.
While the rush to satisfy the emerging 3D market demand for a performance alternative to ABS substrates has spawned numerous products and suppliers, NatureWorks says it is concerned that some companies may not have the Ingeo materials and processing expertise of 3DOM, or its quality control equipment such as continuous online laser scanning. Without the deep technical knowledge specific to this polymer substrate, new grades of filament that could advance the industry may never reach manufacturers or end users.
“With Ingeo, 3DOM gives people the freedom to create without the hurdles and frustrations of markedly inferior monofilaments,” says 3DOM director Daniel McMenamin. “We’ve spent a year developing a process for converting Ingeo into a consistently high quality filament portfolio. We have all the primary colours and will be working on others.”
He added that because 3DOM is intimately familiar with the entire portfolio of available Ingeo grades, it can tailor Ingeo monofilament properties such as stiffness or finished part impact resistance and dimensional stability to best suit the end product requirements.
At the Ingeo Takes Root conference, Ingeo PLA also received total endorsement from Stratasys – the leading manufacturer of 3D printing technology, which recently acquired the MakerBot low-cost system aimed at consumer enthusiasts.
Stratasys director Jim Orrock said that PLA was initially chosen as a sustainable and recyclable/compostable material, but has subsequently excelled in terms of the design freedom it allows in terms of its ease of processing through the company’s printing heads and its robustness in the non-heated build-up of 3D printed structures.
This is a story which will continue to unfold in the next few years, with the potential to change manufacturing practices and products.
Business intelligence for the fibre, textiles and apparel industries: technologies, innovations, markets, investments, trade policy, sourcing, strategy...
Find out more