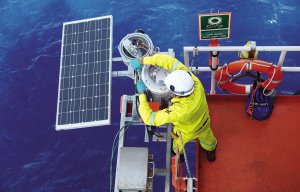
Durability is the key with Extreme X
Aluminium and copper furnaces operate at temperatures of between 800-900°C, and steel furnaces can run at temperatures above 1,600°C.
7th April 2021
Innovation in Textiles
|
Kernersville, NC, USA
CarbonX FL-100A is an aluminized fleeced knit produced by Tex Tech Industries of Kernersville, North Carolina, designed for the ultimate protection of workers in extreme environments.
Aluminium and copper furnaces operate at temperatures of between 800-900°C, and steel furnaces can run at temperatures above 1,600°C. In these extreme conditions, the PPE must shield workers from the potential metal splash of these extremely hot materials, and they also protect against the staggering amount of radiant heat that is generated by the metal and furnaces.
Ideally, workers also need to be comfortable, allowing them to safely complete their strenuous tasks while working in such extreme conditions.
The most widely used fabrics for protection against molten metal utilise thin aluminium laminates on their surfaces. The aluminium exterior reflects much of the radiant heat generated by the metal and/or furnace, allowing personnel to work in close proximity to these industrial heat sources. Aluminized fabrics are the standard components for this type of exposure.
CarbonX FL-100A is lightweight and flexible, and therefore a relatively comfortable option for protection against metal splash. However, as with almost all other aluminized fabrics, the aluminium film used in laminating the outside of these fabrics is a solid layer, and therefore non-breathable.
To create a more comfortable aluminized fabric, CarbonX Breathable Aluminized combines the required level of protection while elevating the comfort via moisture wicking and breathability.
To create a moisture wicking substrate the company combined a multi-layer nonwoven felt as the base fabric, consisting of a layer of hydrophobic fibres and a second layer of hydrophilic fibres.
The hydrophobic fibres do not like moisture, while the hydrophilic fibres love it. The hydrophilic fibres are placed in the layer away from the skin, and because of their orientation in relation to the hydrophobic fibres and the wearer, they pull the sweat and moisture away from the body and to the outside of the garment. A strengthening scrim between these two layers keep the fabric strong and durable!)
Breathability is provided by a special needling technique to perforate the aluminized surface. When the moisture is wicked away from the body via the hydrophilic fibres it can then escape through the holes on the surface of the aluminium. The airflow and the water evaporating after seeping through the holes has a dramatic cooling effect.
While the holes are small enough to allow air permeation, they are not large enough to significantly affect the level of radiant heat protection that the outer layer of aluminium provides. Likewise, when exposed to molten splash, the holes are small enough and the metal splash hot enough that the holes seal when hit with molten metal. The perforated fabrics still meet the ASTM F 955 standard, which is the standard test method for evaluating heat transfer for protective clothing on contact with molten substances.”
Business intelligence for the fibre, textiles and apparel industries: technologies, innovations, markets, investments, trade policy, sourcing, strategy...
Find out more