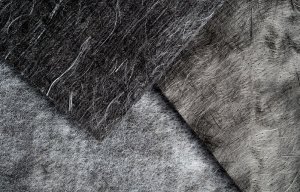
Interview with Marco Gehr, Chief Operations Officer, ELG Carbon Fibre
Innovation in Textiles talks to Dr Topher Anderson, Technical Embroidery Manager at ZSK USA.
17th September 2018
Innovation in Textiles
|
Dornbirn
Innovation in Textiles talks to Dr Topher Anderson, Technical Embroidery Manager at ZSK USA Inc., on the opportunities for optimising carbon fibre composites with tailored fibre placement (TFP).
What are the key problems faced by carbon fibre composite manufacturers, in trying to drive down costs and optimise their processes?
Topher Anderson: While the price of carbon fibre has been rapidly falling in recent years, it still remains an expensive and highly sought-after material. Carbon fibre composite material properties such as a high strength-to-weight ratio are increasingly being sought for the next generation of fuel-efficient transportation. Decreasing the weight of a vehicle, plane or spacecraft can significantly impact its fuel efficiency over its expected lifetime. Increasingly, carbon fibre is being researched as a replacement to some aluminium structures, specifically due to the weight savings it holds. However, the high upfront materials cost of carbon fibre composites can dissuade potential users from adaptation.
In addition, the manufacturing of traditional carbon fibre composites has required more processing involvement than aluminium.
In processes such as resin transfer moulding (RTM), for example, woven carbon fibre fabrics are traced in CAD, cut to scale, wetted with matrix material and allowed to cure to shape. However, such processes are often more labour intensive, and lack the automation seen in competing processes such as metal milling or sheet metal bending.
You have identified a number of specific areas where TFP can make a difference, including waste reduction. How much of an issue is this?
TA: One of the leading material costs of many traditional carbon fibre composite construction techniques is the large amount of waste material generated. In many hand lay-up processes that use carbon fibre woven material, waste material can easily account for 50% or more of the total weight of carbon used. This waste is generated as the fabric is initially being cut, before impregnation with the matrix material. Additional waste is generated after the composite has been cured and during the post processing steps where the shape is further refined.
TFP is unique in its ability to reduce waste material and thereby optimise material cost. By controlling the path of the tow material as it is stitched into the desired geometry, material is only placed where it is needed in the final preform. Areas of fabric that would have to be cut out in traditional laminate design are simply left unstitched. This process reduces both the initial waste produced when cutting woven fabrics to shape, and also post processing waste, due to the ability to conform to complex geometries.
What advantages are there in the creation of hybrid carbon and glass fibre composites via the TFP route?
TA: An additional drawback of traditional laminate processes is the inability to rapidly change materials volumetrically, to benefit from their combined advantages. TFP is a method for quickly and effectively creating these multi-material composites.
For example, when a structural analysis is performed on a part, it might be discovered that the part only requires areas of localised stiffness. In this case, carbon fibre, with its high stiffness, can be placed exactly in the areas and geometries of the part requiring this performance. It would be inefficient to fill the entire part with highly stiff carbon fibre, especially when that stiffness is not required in certain locations. Therefore, to further reduce cost, the areas around the carbon fibre-stiffened geometry can be filled in with lower cost materials such as glass fibre, or even hemp. TFP allows these material transitions to be made seamlessly.
What about design optimisation?
TA: One of the largest benefits of using TFP is the ability to precisely control where each tow of carbon fibre is placed in a design. This allows the designer to further optimise properties, reducing the need for additional material.
For example, complex tow paths of carbon fibre can be embroidered to perfectly resist the applied loads. By aligning fibres to their principal stresses, additional mechanical support is provided without using additional material. Further optimisation can occur by selectively reinforcing holes and circular drill points. In traditional laminate design, these holes can serve as areas of crack propagation due to the orthogonal nature of the woven fabric used. TFP can be used to selectively reinforce these holes with curvilinear patterns, reducing the effective initial crack propagation locations. This can allow for a thinner material at the hole’s location, and even potentially the removal of metal reinforcing washers.
There is also the opportunity to tune the thickness locally. What are the benefits?
TA: In traditional laminate design, carbon fibre composites are presumed to have even thickness. However, TFP does not have such a height restriction. In combination with well-designed moulding and fixtures, carbon fibre preforms can create localised thickness in highly complicated and varied geometries.
Localised areas of height can be created with TFP to better resist bending at the specific location. This optimisation allows for decreased material usage to achieve the same, if not improved, bulk material properties when compared to other composite processes.
What about cycle times – one of the drawbacks of traditional composite laminate manufacturing can be the long cycle times required to properly cure a thermoset resin?
TA: Comingled fibres – where a carbon fibre tow has additional thermoplastic matrix materials added directly into its fibre structure – have been created to reduce processing times.
These comingled materials can be stitched in the same manner as other TFP composite materials. However, these preforms can also be quickly thermocycled in heated presses to rapidly reduce the cycle processing time. Traditional thermoset composite materials using resin transfer moulding can require between 30 minutes to 40 hours to properly set and cure a single piece.
TFP of comingled materials allows for the placement of both the reinforcing fibre and the matrix material in the same preform. As the preform is heated, the liquid matrix is distributed directly into the carbon fibre, allowing proper wetting. The TFP of comingled fibres eliminates the need for additional resins and can significantly reduce materials cost. Additionally, the desired fibre-to-volume fraction is created during the comingling step, increasing the uniformity of the composite material from batch to batch.
These comingled fibre composites represent a step towards a more sustainable carbon fibre composite due to their ability to be re-melted into new forms at the end of their lifecycle.
Doesn’t TFP also allow production designs to be changed rapidly?
TA: Yes, to the extent that a machine can seamlessly transfer from producing car parts in the morning shift to sporting equipment in the afternoon shift.
Additionally, TFP can allow the same machine to produce one prototype design at a time to investigate a process and troubleshoot it without wasting excess material, to creating a full production run simultaneously. This rapid prototyping to production capability, in combination with the ability for a machine to run many different types and geometries of parts in rapid succession, allows for more versatile projects to be run on the same machine. This reduces the cost of setting up a new machine each time a new design is generated.
In conclusion, the six methods of optimisation for carbon fibre composites we’ve covered show some of the advantages of TFP over traditional composite processes. It is hoped that the combination of these optimisation methods, in conjunction with a trend of decreasing carbon fibre material costs, will allow a new class of ubiquitous and highly engineered materials to further improve consumer use cases like fuel efficiency.
Business intelligence for the fibre, textiles and apparel industries: technologies, innovations, markets, investments, trade policy, sourcing, strategy...
Find out more