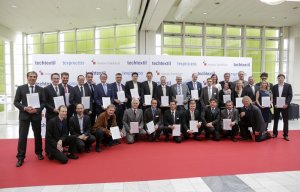
Texprocess Innovation Award 2017 to honour latest developments
Opinion
The garment making-up industry has always been the labour-intensive ‘bottleneck’ of the conventional textile chain, despite attempts such as the Leapfrog EU7 project to streamline and automate all of its processes into a single-line system.
17th June 2013
Adrian Wilson
|
Frankfurt
The garment making-up industry has always been the labour-intensive ‘bottleneck’ of the conventional textile chain, despite attempts such as the Leapfrog EU7 project to streamline and automate all of its processes into a single-line system.
It’s pretty much the same for many technical textile fields too: fabrics that can be woven or knitted in thousands of metres by a single machine in minutes often have to be painstakingly converted by armies of separate machinists, who, however skilled, can still be amongst some of the lowest paid in the world.
Now, however, things seem to be changing and the move to much higher automation – with its attendant high output and resource-efficient practices – is spreading to even the least developed textile manufacturing centres globally. Mass customisation is still poised to take things a stage further too, once it finally gains critical mass in the market.
“By relocating production plants around the world further away from Europe and North America and with raw materials prices falling, the garment industry has been in a position to continuously reduce production costs,” points out Günter Veit, CEO of Veit, a leader in technology for the ironing, fusing and pressing of garments headquartered in Landsberg/Lech, Germany. “Now this has reached a limit. It’s becoming less possible to further reduce either wages or the costs of material anywhere in the world.”
In the future, Veit says, all garment manufacturers will be forced to declare their CO2 emissions and consequently, there is a huge potential for lowering energy costs. The company’s eMotion package combines centralised energy, machine-specific insulation and intelligent programme control. Retrofitted to existing machines, it can save up to 40% in heating energy costs and involves making just a few easy modifications.
Veit was just one of the 330 exhibitors at Texprocess 2013, held alongside the Techtextil show in Frankfurt, Germany, from June 11-13, to showcase the future of textile making up – whether for garments or technical textiles going into industries such as automotive, geotextiles, filtration and protective clothing.
Germany’s VDMA held a press conference during the event to further emphasise the advantages of the adoption of energy efficiency and resource saving measures, which it is promoting under its BlueCompetence programme.
An example selected was the Pfaff 2590 large-area automatic stitcher which can be employed on materials such as high-end leather car seats. Just one needle stitch out of place renders a piece of leather with a value of around 40 euros unusable, since reworking it is difficult, if not impossible. The Pfaff unit’s sensor controlled seam monitoring system ensures 100% reliability and it can also replace between three and five conventional stitching units, resulting in significantly lower power consumption.
Technology has meanwhile been adopted from the nonwoven hygienic disposables industry for the latest BM-1000 bonding machine, which received a Texprocess 2013 Innovation Award.
Brother MD Valerio Scotti explained that while operating just like a conventional sewing machine, it combines the adhesive application and the pressing of seams in a single operation, making it much faster and easier than the existing method of tape bonding. The products are fully stable after 24 hours and can be stretched and washed. The high efficiency of this machine suggests it has a bright future in the replacement of either sewn or tape-bonded seams, especially in applications such as sportswear.
The progress being made in the area of rapid prototyping and 3D visualisation was demonstrated by Human Solutions Assyst. This company’s integrated technology is allowing significant savings to be made along the garment design chain through Cloud-based interaction. Its 3D simulation programme displays all details as if they are already sewn and it can even fasten or unfasten buttons. Not surprisingly, the technology is being widely adopted by, among other industries, global automotive platforms for the design of interiors.
The company’s new Grafis CAD system can even carry out precise body measurement from individual digital photos, taking the interactive nature of mass customisation a stage further.
Texprocess 2013 opened up a world far removed from the traditional notion of the garment making ‘sweatshop’.
Business intelligence for the fibre, textiles and apparel industries: technologies, innovations, markets, investments, trade policy, sourcing, strategy...
Find out more