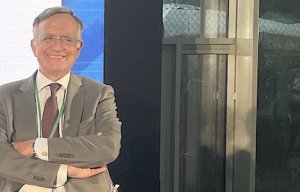
New general secretary at Cematex
Chinese companies have not surprisingly moved into the production of nonwovens manufacturing machinery in a big way over the past ten years, and at the recent ITMA Asia + CITME show in Shanghai, virtually outnumbered the established names in this field from West Europe. They included Jiangsu Yingyang Machinery, which is located in Changsu, near Shanghai and has been developing its extensive machinery range for the past decade. It includes both drylaid and spunmelt syst
9th July 2010
Innovation in Textiles
|
Shanghai
Chinese companies have not surprisingly moved into the production of nonwovens manufacturing machinery in a big way over the past ten years, and at the recent ITMA Asia + CITME show in Shanghai, virtually outnumbered the established names in this field from West Europe.
They included Jiangsu Yingyang Machinery, which is located in Changsu, near Shanghai and has been developing its extensive machinery range for the past decade.
It includes both drylaid and spunmelt systems, as well as all bonding technologies, and the company is not just selling to its domestic market, but already has installations in Australia, France, Greece, Russia, Saudi Arabia and South Africa.
China High Tech Heavy Industry, meanwhile, based in ZhengZhou, in Henan Province, was promoting spunlaced nonwovens equipment for products in the weight range of 35-220 gsm.
Changshu Feilong Machinery was a third company showing an extensive range of machines for nonwovens production.
This company introduced the first China-made 6.6-metre-wide needlepunching line for geotextiles and automotive products, as well as a hydroentanglement unit, over a decade ago, and has also exported machines, notably to South Korea, Russia and Thailand.
Lars Brucker of needle specialist Groz-Beckert confirmed that China’s nonwovens sector is currently booming, with entire ‘nonwoven cities’ being established.
Four months ago, Mr Brucker moved to Yantai as the technical sales manager for the nonwovens division of Groz-Beckert in China solely to be able to offer hands-on assistance to the many needlepunch customers the company now has in the country.
At the 2009 Insight conference held in Memphis, Tennessee, USA, Warren Collier of consultancy John R Starr made some illuminating observations on how the global nonwovens market – worth an annual US$25 billion, equating to seven million tons of product – has developed in recent years.
Chinese nonwovens production in 2008, he revealed, was 1.35 million tonnes, having grown at 17-20% per year for the last 30 years. Domestic Chinese consumption is increasing to make up for lower exports.
Spunmelt production overtook drylaid in China by 2008, reaching 650,000 tonnes, or about 50% of total nonwovens, according to the China Nonwovens Technical Association (CNTA), while airlaid and wetlaid combined constitute only 5% of this market at present.
Industrial end-uses are still the largest Chinese nonwoven market with 39% of the total, but this will soon be overtaken by medical, health care and hygiene – currently 29%, but growing at 26% a year compared to industrial growth of just 8%.
The growth of Chinese spunmelt between 2007 and 2008 –at 135,000 tonnes – far exceeded the new installations of European machines in China of just 32,000 tonnes and Mr Collier suggested a range of companies who are virtually unknown so far outside China, as the suppliers of the rest.
These include, in addition to the companies already mentioned, Anfu Plastic Machinery, Changlong Machinery, Hongda Research Institute, Shuangwu NW Machinery and Wenzhou CL Import/Export.
Chinese made installations, Mr Collier said, cost about 30% of their European counterparts at the same width, but operate at lower speeds, with lower uptimes.
As a result, they achieve only about 35-40% of the output of a modern European installation at present, and if these developments are troubling the European machine builders, it certainly wasn’t evident at ITMA Asia + CITME.
All of the major West European machinery associations – Germany’s VDMA, Switzerland’s Swissmem, ACIMIT of Italy, the UCMTF in France, Spain’s AMTEX and the UK’s BTMA – reported brisk business at the Shanghai show, and a number of key nonwovens contracts were announced.
Germany, for example, overtook Japan as the largest supplier of textile machines to China in 2009, the VDMA revealed at a press conference in Shanghai.
VDMA textile companies achieved machinery sales worth €1.813 billion in 2009, which was down by 40.3% on 2008 – and from sales of €3.8 billion in record-breaking 2007 – but orders have happily bounced back this year.
“First quarter sales for 2010 were up 17.7% on the comparable period of 2008, at €279 million, with almost 85% of this achieved in just six countries,” said managing director of the VDMA’s textile machinery association, Thomas Waldmann. “This once again confirms the dominance of the major Asian manufacturers, and especially China.”
In 2009, Asia accounted for €1.050 billion and China alone €628 million of German textile machinery sales, followed by those worth €452 million in Europe, €477 million in North America, €111 million in Latin and South America and €47 million in Africa.
And meanwhile, on a very small booth tucked away in a corner of the show, a small German company was promoting a comparatively new technology that has the potential to be massive in China.
The Nanoval process, developed by the Berlin-headquartered company of the same name, is a method of either totally or partially splitting monofilaments to obtain much finer filaments – approaching the level of nanofibres.
In the Nanoval process, a melt filament extruded through a spinneret is seized by air streams flowing in parallel but at ever increasing speed, causing the filament to eventually disintegrate, or explode.
And the beauty of this process is that it enables the creation of much finer fibres than is possible with meltblowing and at high capacity on robust and standard equipment.
Bico or multicomponent fibres are not required if all that is desired are finer diameters, and the process is suitable for all polymers, for the production of fibres of below one micron.
China’s rapid progress in becoming the world’s largest producer of polyester is well known – it produced 26.3 million tons of man-made fibre in 2009, of a global total of 44.1 million tons.
By 2000, China was already producing 30% of the world’s polyester and in 2010 its share is 65%, with eight of the leading producers in the top ten being situated there.
But what is also well known is that there is a tremendous amount of unused fibre capacity in China – a situation exacerbated by the recent recession – and not just in polyester, but in nylon, acrylic and spandex too. This has led to allegations of dumping by Europe and other trading partners against Chinese mills.
Nanoval offers the opportunity for Chinese producers of standard synthetic fibres to switch to higher added-value products which are, as yet, not commonly available in the country, at a reasonable outlay.
Little wonder that its booth at ITMA Asia + CITME was constantly packed.
Business intelligence for the fibre, textiles and apparel industries: technologies, innovations, markets, investments, trade policy, sourcing, strategy...
Find out more