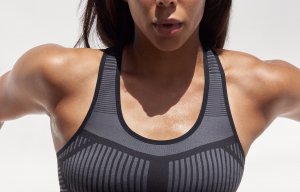
Nike’s first Flyknit apparel innovation
Flyleather is a sustainable material developed as a result of the brand’s partnership with Eleather, based in Peterborough, UK
17th September 2020
Innovation in Textiles
|
Beaverton, OR
Since their introduction eight years ago, Nike’s Flyknit seamless knitted uppers have revolutionised the sports shoe sector, cutting considerable amounts of waste and improving production efficiencies while leading to new levels of wear and while spawning thousands of imitators.
Over the past three years, however, another Nike footwear product has been gaining quiet momentum – Flyleather, a sustainable material developed a result of the brand’s partnership with Eleather, based in Peterborough, UK.
Nike has just launched a new version of its Janoski skate shoe made based on the material innovation.
ELeather
As an alternative to leather, ELeather is already employed by over 200 airline companies and in addition, around 12,000 trains and 12,000 buses have been upholstered with it.
ELeather is not an artificial leather made from microfibres, but instead is composed of a recycled fibre that is made from chopped up waste leather shavings that are normally sent to landfill.
It is 40% lighter than conventional leather and manufactured by a patented process adapted from the airlaid and hydroentangled production routes for making nonwoven fabrics. This involves altering and grinding the waste leather trimmings and split hides to produce individual leather fibres.
Partnership
Nike announced a long-term, strategic innovation partnership with ELeather back in 2017 to coincide with the first commercial launch of a Flyleather product – the Nike Flyleather Tennis Classic. It has subsequently introduced a number of ranges featuring the material.
Flyleather shares its sustainability credentials with ELeather’s other engineered leather products by not only saving thousands of tons of leather offcuts from ending up in landfill, but also using less water in the manufacturing process.
It is also 40% lighter and five times more abrasion resistant than traditional leather, but also improves cutting efficiency thanks to the fact that it is produced on a roll as opposed to an irregularly shaped hide.
This is a great benefit to Nike considering that leather, as a material, has the second-highest environmental impact on the company’s carbon emissions and water usage. By introducing Flyleather into the mix, Nike has been able to not only introduce a new material but also improve its sustainability credentials.
Business intelligence for the fibre, textiles and apparel industries: technologies, innovations, markets, investments, trade policy, sourcing, strategy...
Find out more