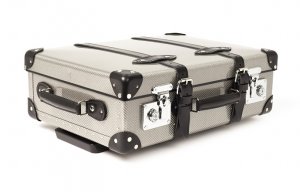
F1-inspired carbon fibre case launched
Novel supermicro fibres based on cellulose and cellulose-2.5-acetate are being developed at ITCF Denkendorf (the Institute of Textile Chemistry and Chemical Fibres) in Germany.
9th October 2012
Innovation in Textiles
|
Dornbirn
Novel supermicro fibres based on cellulose and cellulose-2.5-acetate are being developed at ITCF Denkendorf (the Institute of Textile Chemistry and Chemical Fibres) in Germany.
The key to their success lies in the parallel work of the IFSW (Institute of Laser Tools) in Stuttgart, which is enabling the ultra short pulsed laser radiation drilling of superfine spinnerets through which these new fibres can be extruded.
At the recent Dornbirn Manmade Fiber Conference in Austria (September 19-21), Franz Hermanutz of the ITCF explained that the IFSW’s new technology is based on helical laser drilling – with the beam rotating just like a conventional drill.
A large variation of spinneret materials and spinneret hole dimensions is possible and the outlets of the spinnerets are especially fine and smooth.
The fibres subsequently produced at ITCF can’t be produced by conventional bicomponent spinning (the joint spinning of fibre and matrix components followed by chemical dissolution of the matrix) or electrospinning. Nevertheless, they are expected to have useful applications in both nonwovens for hygiene and woven and knitted textiles for technical applications.
A new wet spinning technology based on these superfine spinnerets – which have approximately 2,000 channels over the area of the globe on a one euro coin – has been developed. The cellulose is processed in ionic liquid and the cellulose-2.5-acetate processed in acetone. Both are thermally stable and non-toxic and over 99% of either solvent system can be recovered after the process.
The resulting fibres have been successfully wound onto bobbins and yarns of different sizes have been produced from them knitting and woven fabric production is currently being trialled.
Business intelligence for the fibre, textiles and apparel industries: technologies, innovations, markets, investments, trade policy, sourcing, strategy...
Find out more